Innovation sometimes comes from too much perspiration – that was true with Aligni. As real engineers designing and manufacturing electronic products, we realized we were spending too much time searching for parts and components. Then, once the product was designed, turnkey outsourced manufacturing proved to be unnecessarily expensive (and not very good at procurement anyhow!). There had to be a better way that did not include buying onerous software suites currently available.
By Engineers For Engineers
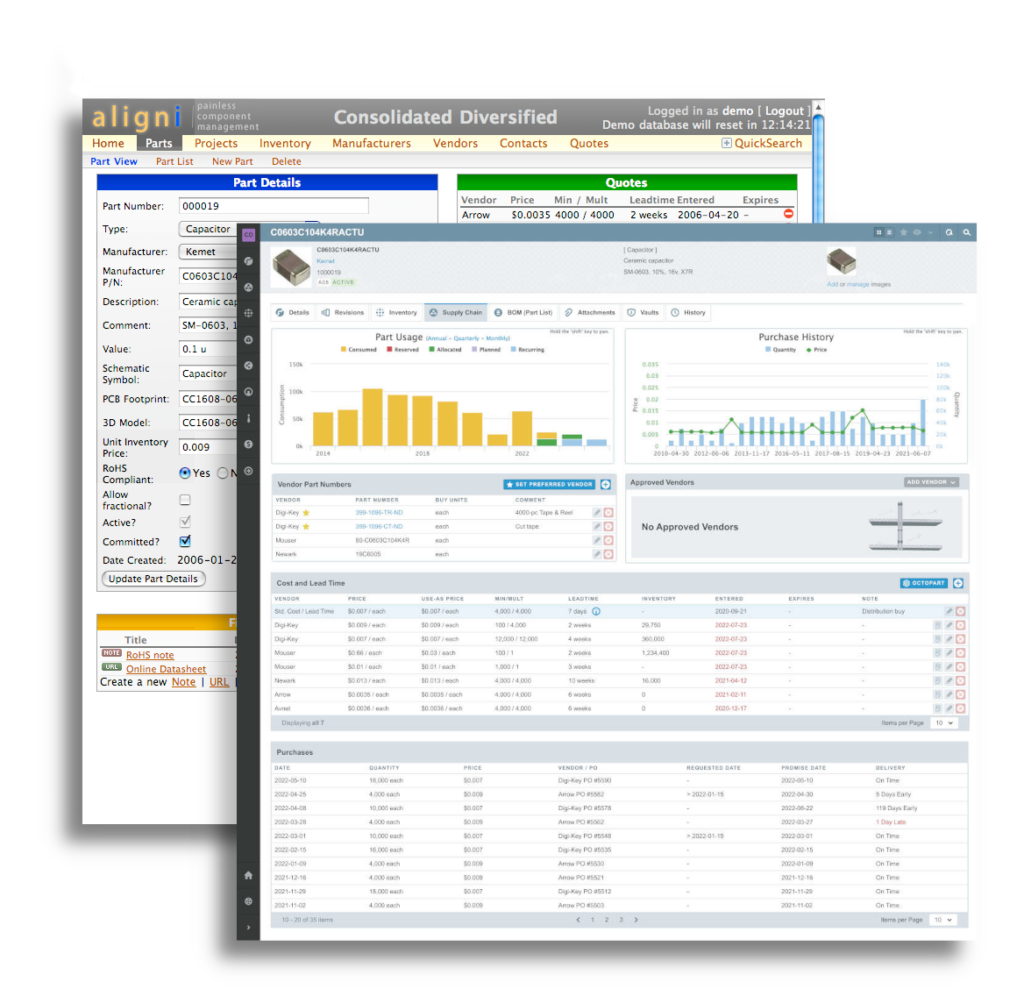
In 2005, there was little on the market that addressed our needs, so we decided to build our own solution from the ground up. From the beginning, Aligni was going to be different. It was going to be cutting edge. The software would be built upon a relational database and written in modern programming languages with easy to use interfaces. Not only that, but it would be cloud-based – a state of the art technology for the time that put Aligni ahead of today’s SaaS trend by decades.
But first and foremost, Aligni was built by engineers for engineers. From the start it needed to provide an easy-to-use, web-based, database solution for managing components, parts, vendors, assemblies, BOMs, and inventory. It would manage this information from the product development process, through manufacturing, and extend to outside vendors. Aligni would be our single source of truth.
We created Aligni to:
- Improve component reuse and reduce part search time
- Develop stronger relationships with our component vendors
- Effectively manage part inventory and production scheduling
- Provide the foundation needed to move from expensive turnkey contract manufacturing to less-expensive consignment manufacturing
A Fresh Look at Part Management
Once we had Aligni up and running, we discovered that the combination of our software and the features of on-demand computing resulted in some spectacular benefits. Aligni eliminated hours of “wasted” time while improving collaborative work and dramatically increasing productivity.
The part selection process was greatly streamlined by a well-maintained item master. Known parts were reused and it was quickly apparent if a new part needed to be found for a particular purpose. Reusing “popular parts” (parts used within multiple projects) increased volume purchases, reduced costs, and stabilized inventory. Engineers had better parts visibility and made better parts selection decisions.
We realized significant cost and time savings in working with vendors. With better information at our fingertips, better cost/inventory decisions were made. This significantly reduced lead times to new builds. Overall, a better balance was achieved between procurement cost, holding cost, and lead time.
Using Aligni helped us dramatically reduced expenses by moving from turnkey to consignment manufacturing. With better management of parts inventory, we were able to move from turnkey manufacturing to consignment manufacturing. This has resulted in both less expensive and more predictable flow of manufacturing.
Aligni made MRP so easy that we didn’t miss the procurement services of turnkey manufacturing. Our cost savings from the manufacture of just one product was enough to fund hiring a full-time person to manage purchasing and inventory. But, of course, we didn’t need to because the work burden was only a few hours per month.
Into the Wild
The results were so spectacular that we decided to share Aligni with some of our engineering friends. Their results have been so great that they encouraged us to turn Aligni into a product and share it with you.
Since then, we’ve continuously been improving Aligni and expanding its purpose. This continuous development comes from listening to our customer base as well as our own experiences with the software over these years – yes, we still use it on a day-to-day basis. Follow Aligni’s updates and developments on our blog.
We hope you’ll give Aligni a try – for free! – and we think you’ll achieve these spectacular benefits too. Learn more about Aligni MRP and Aligni PLM products.