PLM
Aligni for Product Engineers
Developing new products or modifying existing ones involves a lot of research, decision making, and collaboration. This makes the process difficult to manage properly with spreadsheets. It also creates challenges in keeping the information accurate and other departments in the loop.
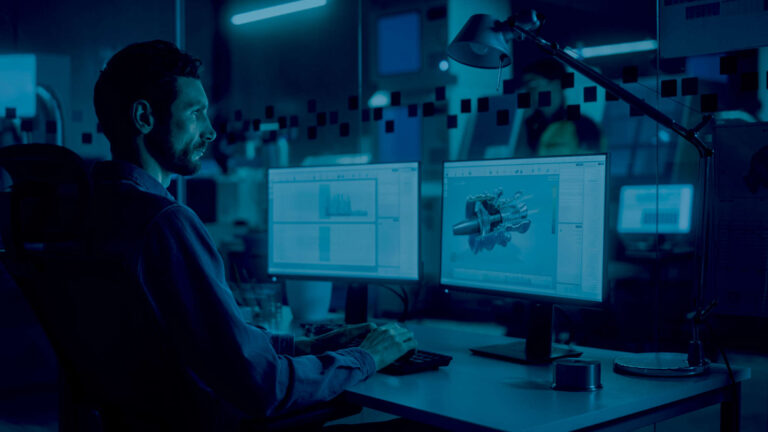
Aligni Product Lifecycle Management (PLM) is purpose-built to handle the tracking of product design information and changes to products and specifications during the product development stage and afterward. The software does this more efficiently than home grown spreadsheet processes because it uses an item master database at its core. This database stores part information, pricing & availability, vendor details, and even interdepartmental decision-making discussions in an easy to update and search manner.
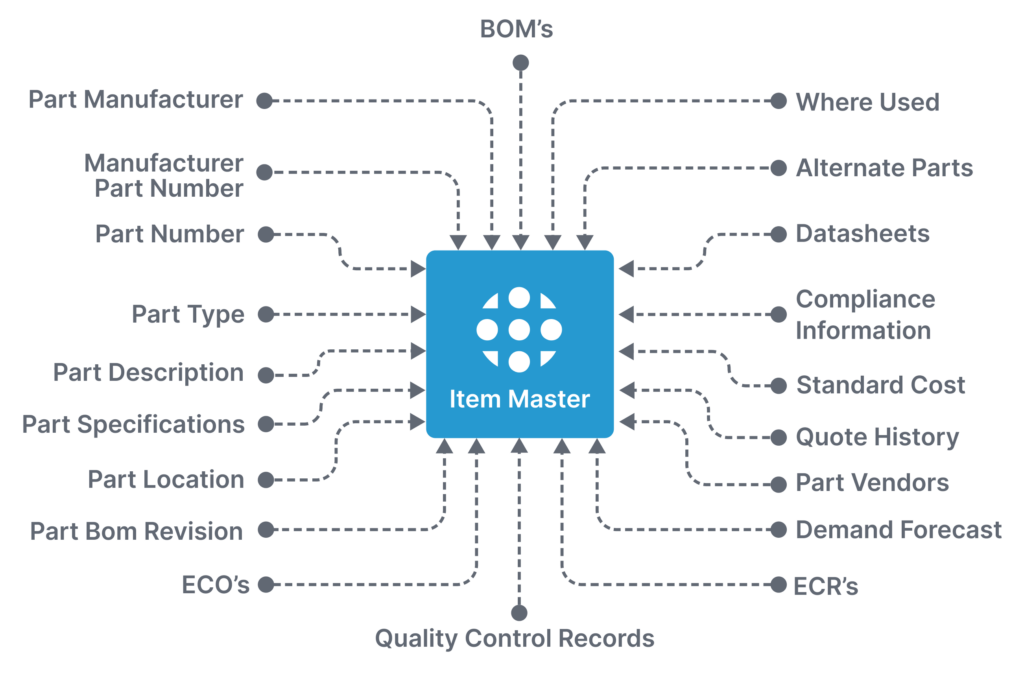
Instead of chasing information across departments and through disconnected files, this database-driven file management approach allows the system to efficiently organize design files, product specifications, and easily manage large amounts of pricing and vendor information. Using Aligni PLM ensures the data is collected in one location, systematized, and made accessible, ensuring a more efficient product development process.
Learn more about the Item Master Database
Understand Component Costs Prior to Production
Hitting product price targets is a crucial component of the product development process. It helps determine if the product will be profitable for the company and whether it will be competitive in the market. As product complexity increases, it becomes more and more difficult to make sure targets are hit and costs remain under control. Aligni PLM provides the ability to manage all of those aspects within its Bill of Materials (BOM) management functionality. The system captures the part pricing and collates it by the quantity of part used to keep a running project total managers can count on to keep projects from spiraling out of control.
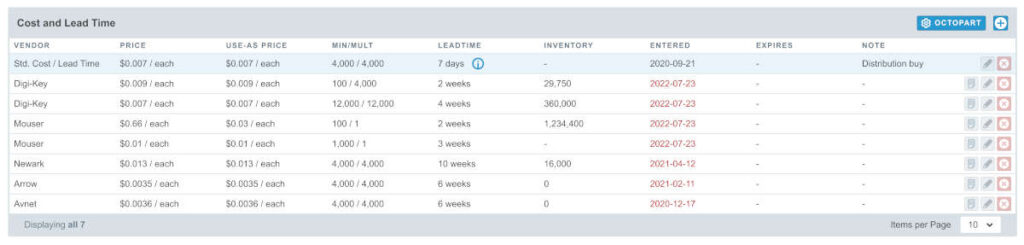
How does the software do this? Aligni calculates build costs from current and previous quote and purchase pricing saved within the system. Engineers and designers do not have to sort through old purchase orders, quotes, or archived email chains to locate the pricing data. Aligni automatically makes the data available by part numbers referenced within the project’s BOM.
Explore Aligni’s BOM management capabilities
Improve Re-Use to Accelerate Product Development
For many companies, product lines tend to have similar functionalities, performance specifications, or customer requirements. That usually leads to potentially higher part sharing between products. Having a searchable database that contains all currently used components can bring benefits to the product development process. Aligni PLM provides just that to engineers looking for the best part for the next product.
Using Aligni’s item master database to store all part and material information for every product, engineers win by being able to quickly search parts already being used elsewhere in the company instead of going outside for every new need. This saves time by reducing the double work of vetting new parts when there may be parts in the system that perform the same function. Engineers also reduce the time waiting to receive part specifications from vendors or test results to prove functionality, as Aligni makes the part information readily available within its item master database.
There is substantial benefit to the purchasing process when previously sourced parts are used instead of finding new ones. Buyers see a reduction in repetitive sourcing efforts for alternative parts. They also may see a reduction in time spent vetting new suppliers for those parts. Depending on total part demand for the new product, buyers may be able to negotiate lower per-unit costs from sourcing larger batches of current parts rather than breaking purchase quantities across a number of parts with interchangeable specifications.
Make Changes with Approved Vendors and Alternate Parts
Product engineers often face challenges when specified parts become unavailable, obsolete, or need to be replaced due to changing customer requirements. Traditionally, finding and specifying replacement parts takes just as much time and effort as the initial selection. However, with the right tools in place to manage existing data effectively, this process can be streamlined, significantly reducing the time and effort required. Aligni PLM can help you access and leverage your organization’s data, enabling faster, more informed decisions when part replacements are needed.
The process of specifying and sourcing parts generates valuable data that can be crucial when changes are needed down the line. During the initial quoting stage, multiple parts and vendors are considered, but only one is chosen for the product. This often leaves viable alternatives unused. Retaining this data allows for a quicker pivot to alternative options when necessary.
Similarly, buyers often continue sourcing materials from new vendors in an effort to secure better pricing or terms. While not all pursuits lead to immediate results, this information can prove useful in the future. Storing and organizing this data ensures quick access when changes occur, reducing the need for redundant work and helping teams respond more efficiently.
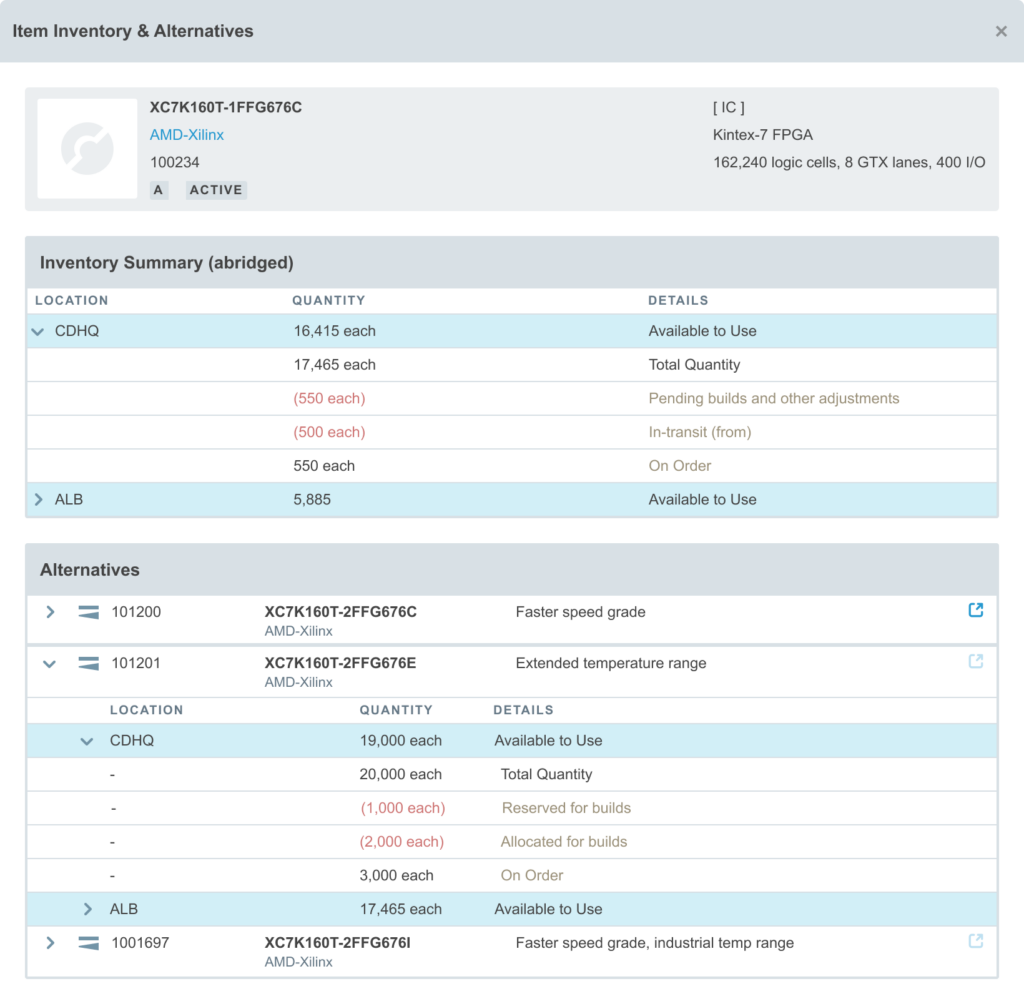
Aligni PLM provides accessibility and storage of alternate part data inline with the specified parts chosen by organizations in the product development and sourcing operation. This alternate part information is available in several places within the software and where engineers and buyers need it most. For example, Aligni lists alternate parts and vendors for those parts within the part details screen. Alternates can also be found through the BOM screen on products in the system.
Using Aligni PLM to manage alternate parts is the best option for a product engineer because it centralizes and organizes critical data, allowing for quick access to alternative components when changes arise. This not only reduces redundant work but also accelerates decision-making, ensuring faster product iterations and a more agile response to supply chain or design challenges.
Learn more about alternate part management in Aligni
Track Changes with BOM Management and ECM Functionality
The process to arrive at a market-viable, cost-effective, and producible product is virtually never a straight-line affair. Requirements change, parts become unavailable, components are found incompatible with others, or other events can derail a smooth development path. Keeping track of all those twists and turns can be almost as difficult as solving them. What makes this aspect of the process easier is engaging a software system designed to handle the complexities of product design: Aligni PLM.
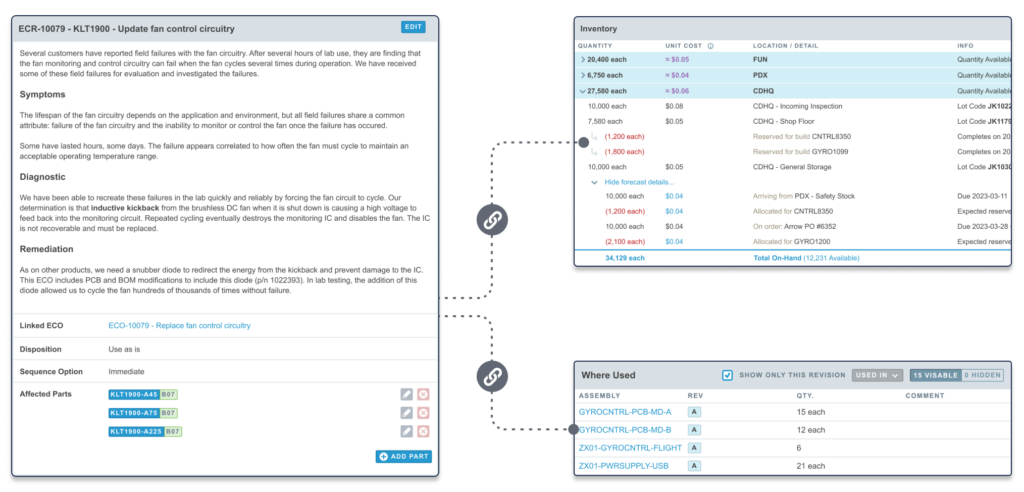
By tracking the changes to a product’s parts list within Algini’s BOM functionality, engineers can not only have an up-to-date understanding of the current condition of the product, but also a searchable record of how the organization arrived at the current revision level.
Going further, Aligni PLM contains integrated Engineering Change Management (ECM) capabilities. ECM processes are another avenue to go into detail recording the changes needed within the product. It’s also a process that other departments within the organization have experience using. Purchasing and quality control personnel are typically experienced with filling out ECRs and ECOs. Digitally integrating these into the product development process provides the company with a better result based on inter-departmental collaboration
Learn more about Aligni’s change management processes
Share Projects Securely and Easily
With Aligni Vaults, organizations can share product information securely with vendors and customers directly from the company’s item master database. No more copying files and data from different folders or applications, double-checking the information is current, and compiling it for sending to external contacts. Instead, the data is selected inside Aligni, the central hub for all part and product data and packaged into a Vault for securely sharing.
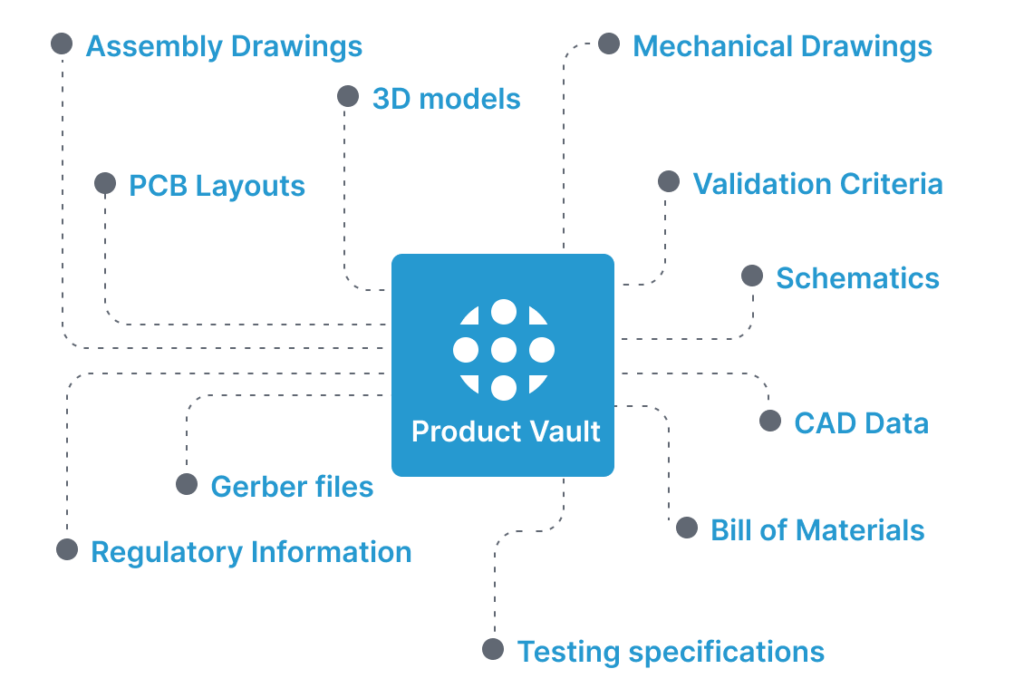
Making changes to shared data is just as easy. Vault updates are immediately transmitted to all who have been granted access. When parts, documents, BOMs or other data are revised in Aligni, these changes are automatically updated within the Vaults containing the information. Users are sent alerts to make sure they are aware of the changes.
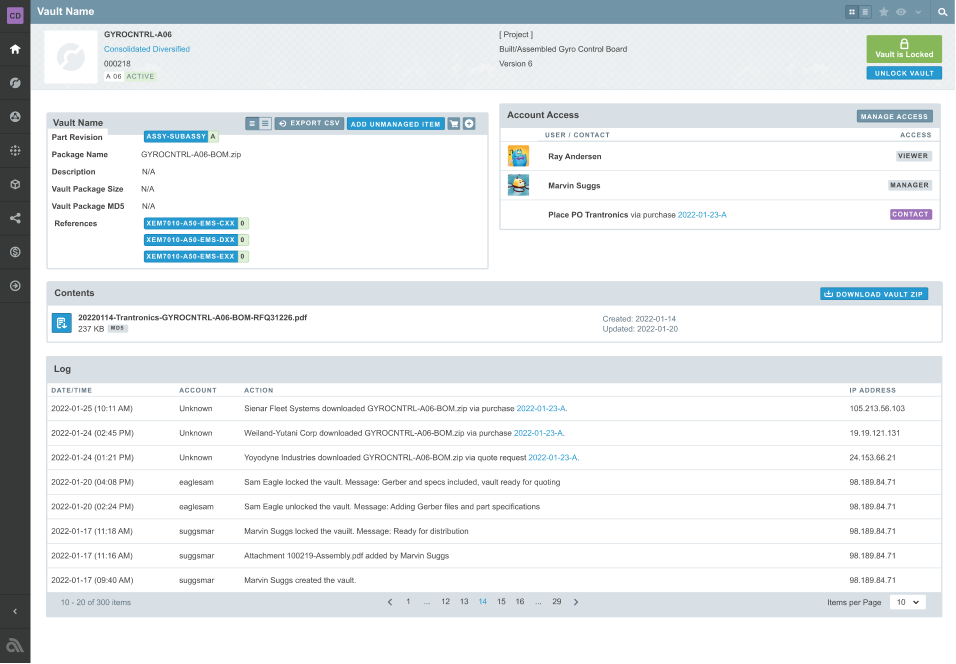
Companies can manage access privileges to shared materials within the Vault. This helps ensure the right people have access to the information. It also provides companies the ability to remove access once the need has passed to share.
Learn more about Aligni’s Vaults
Explore what Aligni can do for your organization
Control the Process… Control Efficiency
New product development can be an exhausting process. It can compound with managing all the parts and information that needs to be tracked within the project. Having the right tools to smooth the process is almost a necessity to not only hit the project specifications but also to make sure it’s done properly and in a timely manner.
Streamline all of it by using Aligni PLM. Sign up online to get started today!
Start your 30-day free trial
Join over 4,000 teams that are managing their manufacturing with Aligni.