PLM
Managing Part and Design Changes with Aligni PLM
Getting a new product to market – or just into production – can be a formidable task. Not having quality management tools in place to help can make it even worse. This is especially true when developing highly complex products with high part counts or ones that are loaded with high-tolerance specifications or certifications to achieve.
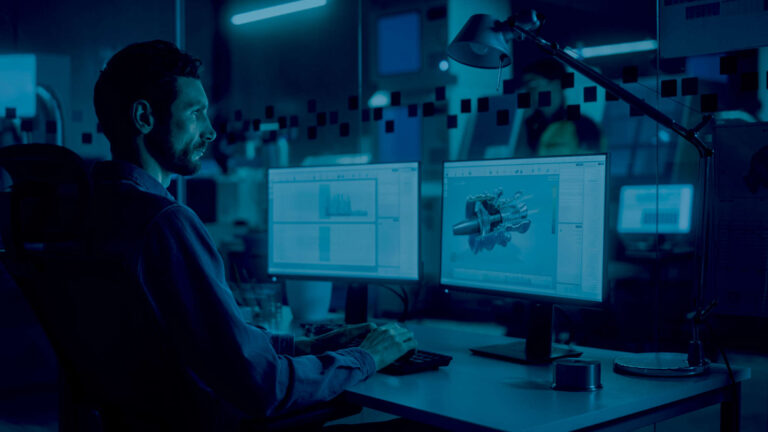
While many believe spreadsheets could be acceptable alternatives, Product Lifecycle Management (PLM) systems are software platforms purpose-built to help organizations manage the entire lifecycle of a product, from its initial development to its eventual retirement. Our Aligni PLM system is a great example of such software.
The Right Tools for the Job
Aligni brings together a number of tools to help engineers and managers oversee all the aspects of specifying, sourcing, and maintaining the parts and materials required to manufacture the product. The Aligni PLM system can continue to manage the needs of the product well into production, service and end of life support. These tools can be helpful in managing part and design changes in the following ways:
1. Centralized Data Management
Aligni’s PLM system provides a centralized repository for storing all product-related data, including part and design changes. Within its item master database, the software makes it easy to track changes and ensures that all team members have access to the most up-to-date information.
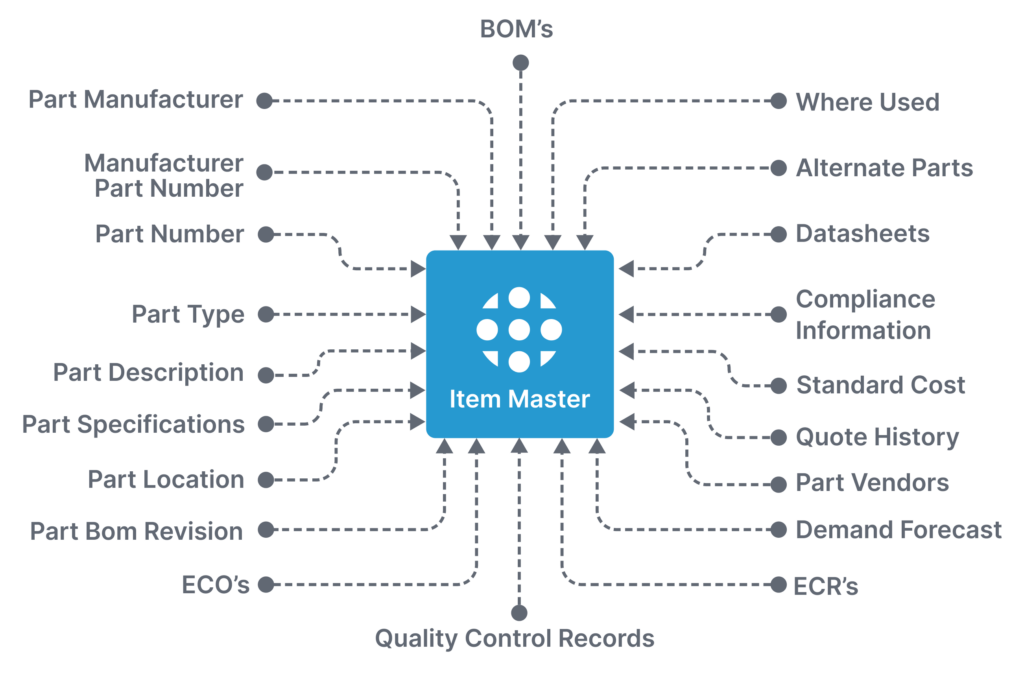
2. Version Control
PLM systems allow you to track changes to parts and designs by creating new versions of the data every time a change is made within the database. Every update to the makeup of the product is held within the system, as well as the reasons for the change and who requested it. This information becomes a searchable archive that maintains the decisions for the direction of the product.
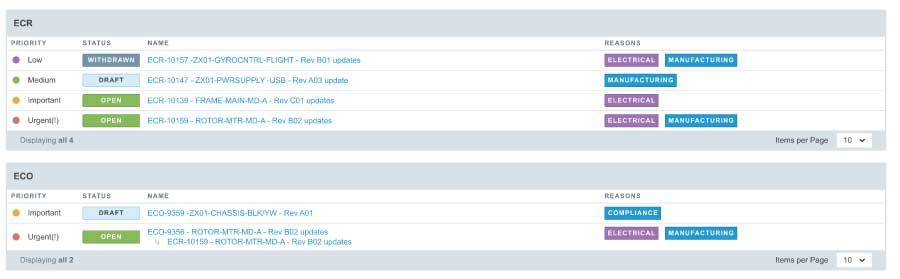
3. Change Management
PLM systems provide tools for managing the Engineering Change Request process for parts and designs. Algini’s ECM tools allows businesses to track the status of change requests and orders, assign tasks to team members, and ensure that changes are properly reviewed and approved before they are implemented. As mentioned previously, the system also maintains records of the process for review at any time.
4. Collaboration
Aligni’s cloud-based PLM system enables collaboration between team members and other departments, regardless of their location. This can be especially helpful when working on complex projects that require input from multiple stakeholders. Everyone works on the same information being held in a single database, rather than independently housing data on their own systems.
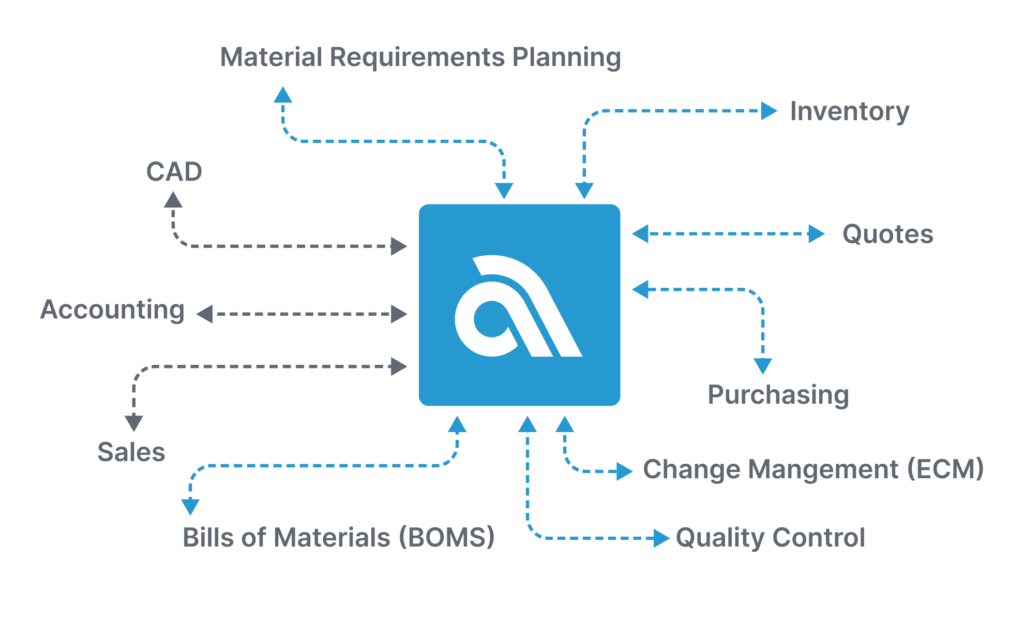
5. Analytics
PLM systems can provide insights into product development processes, such as the time it takes to make changes to parts and designs. By analyzing the development records associated with bringing a product to market, companies can gain insights on its performance and where bottlenecks in the development process may happen. This information can help teams and managers identify inefficiencies and make data-driven decisions to improve the development process for future processes.
Explore what Aligni can do for your organization
Bringing It All Together
For product developers and manufacturers, the benefits of a PLM system’s centralized repository for data, version control, change management tools, collaboration capabilities, and analytics cannot be ignored. Combined, these can have a profound impact on a company’s engineering and sourcing operations, not to mention it’s time to market metrics and overall product quality.
If you’re looking to get to market faster it’s time to manage product data more effectively. It’s time to sign up online for Aligni PLM today!
Start your 30-day free trial
Join over 4,000 teams that are managing their manufacturing with Aligni.