Backcountry Access (BCA) opened shop over 20 years ago in a garage in Colorado. Over the years, it has become the most trusted name, worldwide, in backcountry safety. BCA equips adventurers with both life-saving gear and expertise in exploring the backcountry. BCA’s key product, its avalanche beacon, becomes a transmitter when a person is buried in the snow. With a mission to save lives, not just sell products – product integrity is a life-or-death concern.
BCA’s hardware development lab, purchasing, and accounting teams were using multiple sets of Excel spreadsheets for ordering and managing parts for the development and manufacturing of its avalanche beacons. The large number of parts and part replacements, plus managing multiple contract manufacturers, were making the process increasingly complex and difficult to manage. Multiple Excel spreadsheets just couldn’t keep up.
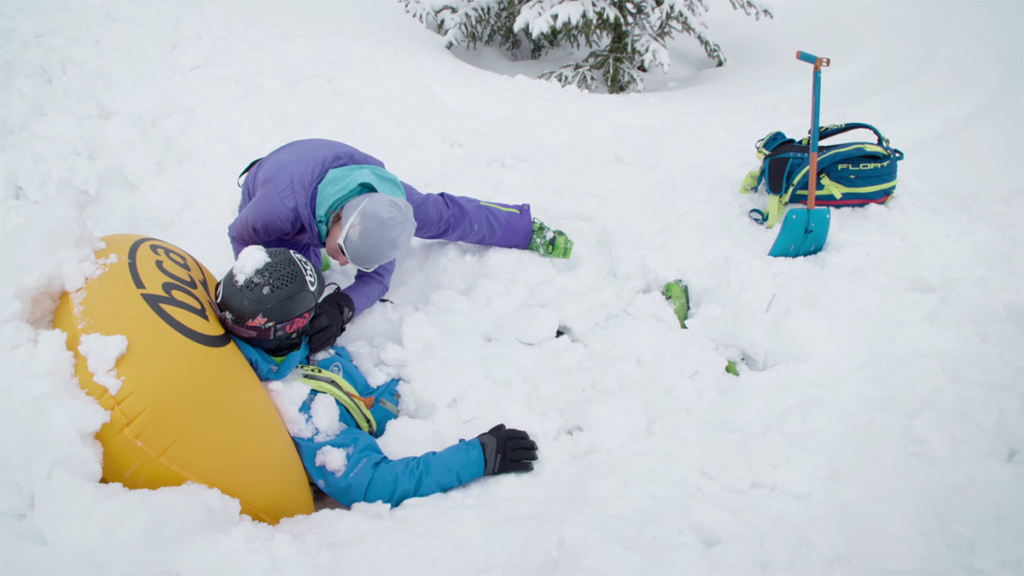
Part Equivalents & Alternatives – a Life and Death Issue
David Van Horn, lead engineer at BCA, said that designing the original beacon is just part of the development team’s role. Once the design is complete and the product is on the manufacturing line, the engineers remain involved to ensure the integrity and safety of each final product.
Over the past two years, the capacitor industry has been cutting down on product lines and consolidating parts. Some capacitors don’t have equivalents, and in mission critical situations, products must be redesigned with alternate parts. “Once you have your product designed, you still have to handle substitute parts, it’s a fact of life,” said Van Horn. “With the current capacitor shortage, I spend a good part of my day looking for substitute parts.”
Being 100% sure that there is an exact match in a replacement component, so that the avalanche beacon will work exactly as designed, is critical when a skier is buried beneath the snow.
David Van Horn, Lead Engineer, BCA.
Solution: Aligni – Cloud-based PLM & MRP
When lives are at stake, careful attention to detail is necessary to assure that safety is always the first priority. Improved auditing and tracking in Aligni can help reduce the cognitive and human resource load required to achieve this goal. This level of audit is achievable with Excel, but only through extensive additional process controls.
BCA uses Aligni to ensure each and every part is monitored and managed from source… to manufacturing… to product delivery. To ensure the integrity of each part, Aligni enables linking of images, files, BOMs, and fabrication data. In addition, replacement parts can be clearly categorized in two ways: “part equivalents” or “part alternatives.” An alternative can do part of the original part’s job but is not the exact same. An equivalent is a validated straight swap out. Van Horn explained, “If you use a gold-plated connector with a tin-plated connector in the same beacon, you will have connection problems. You just can’t have that when you’re trapped under the snow.”
In addition, Van Horn says Aligni makes redesign and traceability much easier. The original design can be left alone, with information added on the variances. If a production batch goes wrong, they have the traceability needed to find and fix quickly.
Aligni has managed to take an ugly, ugly ad hoc parts management process and wrap it up with guidelines and a framework that encourages us to follow the right process, but still gives us flexibility to bypass the rules and make it work quickly if we need to. It’s brilliant.
David Van Horn, Lead Engineer, BCA.
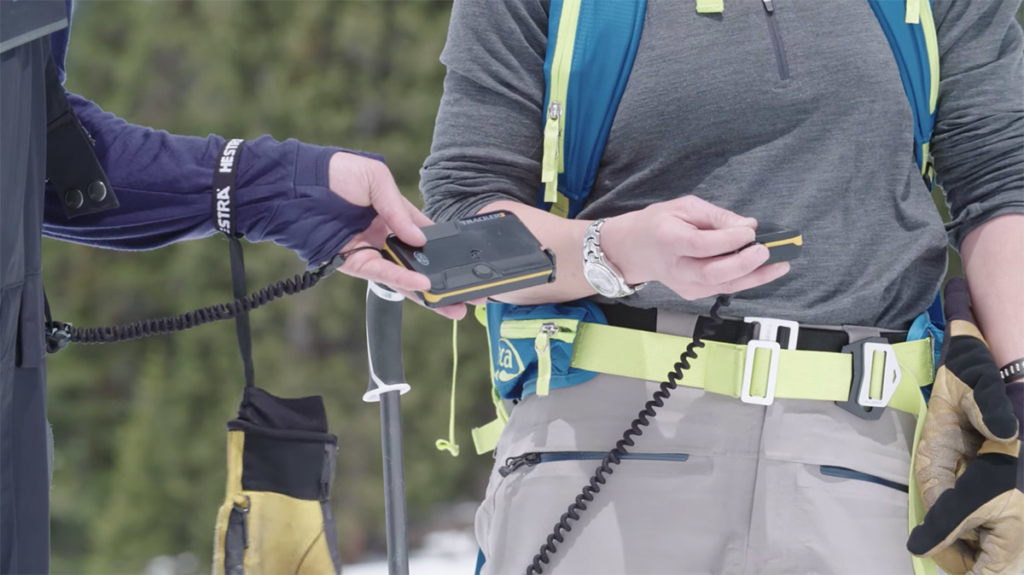
Managing contract manufacturing is a breeze with Aligni. BCA buys and inspects all of its parts, then leverages contract manufacturers to build subassemblies. The BCA team inspects the subassemblies as they are returned, then sends to the manufacturing line for final assembly. “With Aligni, it was trivial to set up the whole hierarchy of parts and sub-assemblies and manufacturing in the system. Using Aligni helped us look at the manufacturing process holistically. We have visibility into the parts and the process from start to finish.”
With Aligni, the whole structure of a given part, manufacturing data, vendor data, line card information, are all linked in beautifully. The ‘best practice’ structure makes perfect sense.
David Van Horn, Lead Engineer, BCA.
Aligni is optimized for multi-site teams managing thousands of parts. For Backcountry Access:
- 360+ parts
- 25 assemblies — for example, a top-level assembled beacon has nine parts, three of which are assemblies.
- 6 inventory locations
- 5 users
- 76 manufacturers
- Two PCB shops and a number of suppliers doing plastics, metal parts, etc..
Aligni at BCA – Unified PLM & MRP
As with many small and medium-sized businesses, a massive ERP system is overkill for BCA’s needs, but Excel spreadsheets can’t come close to doing the job. BCA has found that Aligni is an excellent match for complete and unified parts management – from design through manufacturing and Q/A.
BCA went through years of pain before moving to Aligni. Electronics purchasing is never easy and, for BCA, can mean life or death. “We can’t lose sight of the simple fact that if this doesn’t work, somebody dies,” Van Horn said. “I must know what we did and why we did it. If you know how you got in the hole, you will know how to get out of the hole.”
Aligni is robust, and easy to use. We all have the ability to look at things, but no keys… no one can mess it up. It’s our ‘single source of truth’.
David Van Horn, Lead Engineer, BCA.
Aligni delivers PLM and MRP specifically designed to support development engineers and R&D teams.
- Easy to use: The user interface is straightforward and easy to learn.
- Improved operational intelligence: Documented, factual data sharing.
- Best-practice structure: Organized data and process flows.
- Open API: Enables development company-specific features.
- No lock in: Data always available to company to download.
- Clear, structured, documented communication: ensure precise documentation with contract manufacturers, suppliers and distributors.
- Solid, complete documentation: Prevent errors and unnecessary expense.
- Integration with enterprise ERP or in-house production processes.
- Cloud-based SaaS: All those cloud benefits too!
- Value priced.
- Excellent support (per customer reports).
Aligni works. Everything works. It works well. It does everything they say it does, and more. And it’s easy to use.
David Van Horn, Lead Engineer, BCA.
Have you reached your Excel Tipping Point?
Early adoption of Aligni saves significant cost and confusion, freeing up time and resources for innovation.
About Backcountry Access
Backcountry Access (BCA) has always been about high-performance backcountry riding, starting in 1994 with the Alpine Trekker ski touring adaptor. This product enabled aggressive skiers to “send” backcountry lines not feasible on the telemark gear of the time. Since then, skiing, snowboarding, and snowmobiling have gone to a completely new level of power and athleticism. And avalanche safety gear – BCA Tracker transceivers, Float airbags, BC Link radios, avalanche shovels and probes – have become the ‘must-haves’ for backcountry travel, supporting this new level of athletic talent and dedication to backcountry safety. “At BCA, we don’t just send, we always return.”