Safety Stock Manager
Managing safety stock effectively is an important part of a comprehensive strategy to reduce “line down” risk and keep production running smoothly even with demand surges.
A new safety stock manager is now available to Enterprise organizations. This new approach replaces the simple reorder list functionality with a much richer set of tools. With the new safety stock manager, you can:
- Define different item safety stock targets for warehouse.
- Collaborate with your team on safety stock activity using the new discussion interface.
- See past safety stock activity to help inform changes to range targets.
- Snooze items to temporarily hide items.
- Monitor safety stock status from the inventory dashboard.
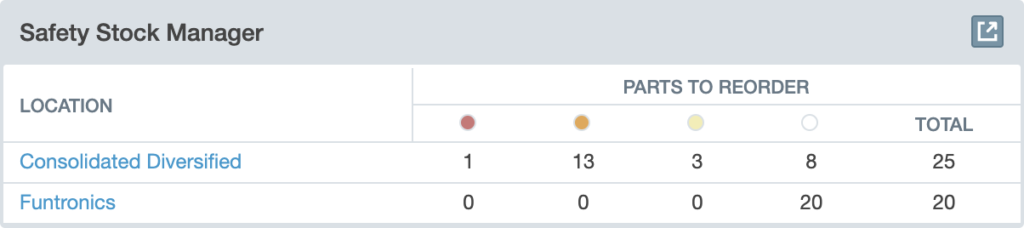
We have a lot more planned for the safety stock manager. These new features should roll out later this year. For more information, please visit our guide on effectively managing safety stock.
Change Management Visual Updates
Change requests and change orders need to be quick and easy to write, review, and manipulate. They also need to communicate a lot of information quickly to be effective. To improve the efficiency of change management records, we reduced the number of tabs and made the presentation more dense. These changes should help your team collaborate more effectively on changes as your products evolve. Briefly, these changes include:
- Tab Removal – All ECR and ECO information is now shown on a single page, reducing clicks and page loads.
- Discussions – Improved visibility of the discussion as well as several visual improvements to make collaboration more efficient.
- Part References – Part references are all shown in the details widget for ECR and ECO. These presentations are also more compact and faster to manipulate.
Build Discussions
In many organizations, a build is on the books for several months as inventory is procured from sources with long lead times. A lot can happen in those months. It’s important to keep your team informed and current on the latest status.
Builds now have a discussion widget to improve collaboration and activity logging. For a lot of organizations, a build can be in progress for weeks or months. With discussions, your team can stop using messy emails and keep everything organized right where it matters. By watching the build using the eyeball icon at the top right of the page, collaborators will receive notifications when someone posts a comment.
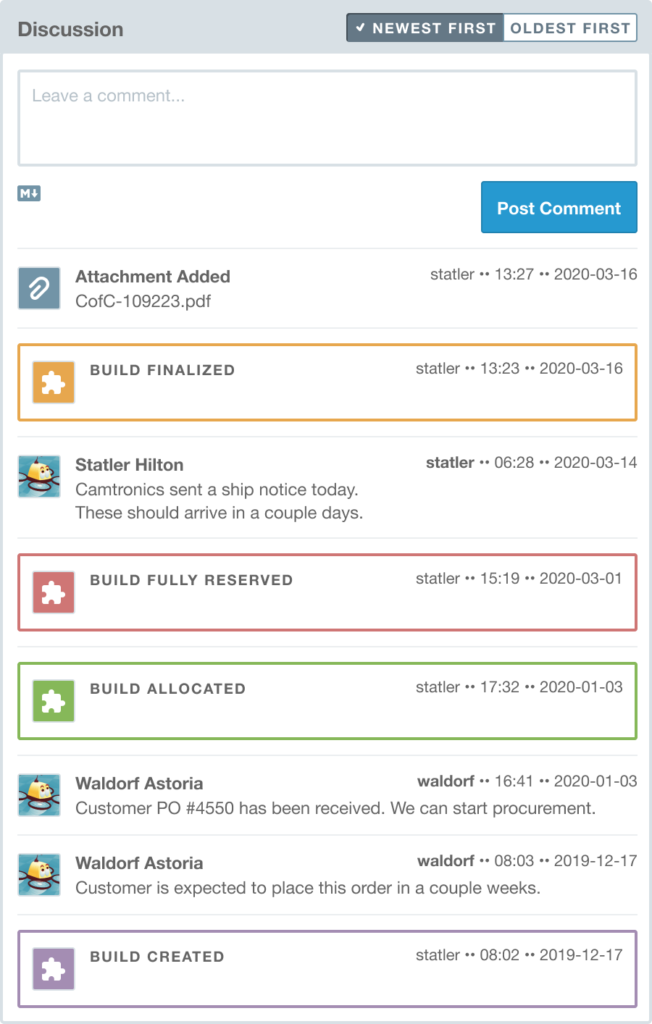
The same discussion interface is used in Engineering Change Management and the Safety Stock Manager. We plan to expand this great new collaboration component to other records in Aligni soon!
Build Deviations Ledger
The new Deviations Ledger is our first major improvement to build deviations. The ledger provides an easier way to visualize and manage deviations for items on a build. In ledger format, the addition, removal, and substitution of items is more readable and clearly indicates the quantity of the item added or removed from the build.
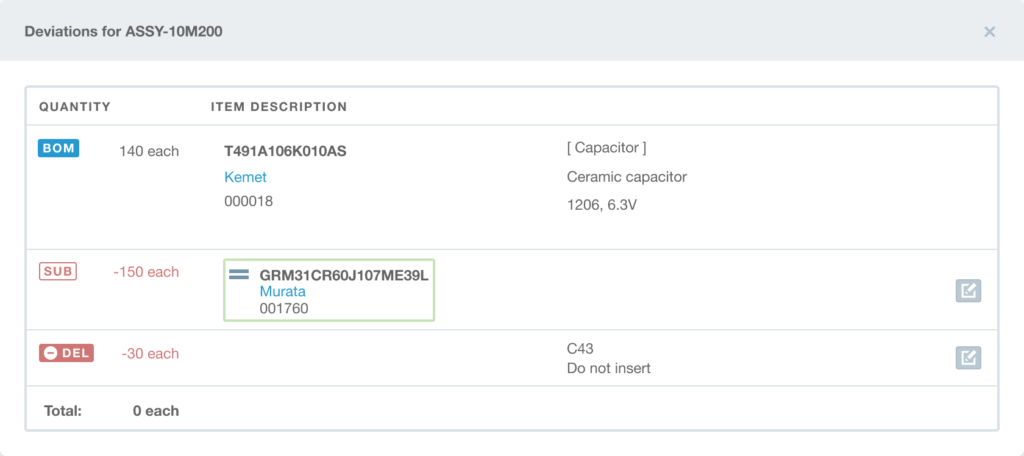
Manufacturer Families
You may now define Manufacturer Families for a manufacturer and add attachments common to that part family in a single location. These common family attachments are then visible to all members of the family on their attachments page.
Family attachments are a great way to collect common information associated with a part family such as datasheets, specifications, regulatory compliance information, or performance data.
Other Improvements
Over the past few months, we’ve made loads of other improvements across all of Aligni including bug fixes, security improvements, performance improvements, and the implementation of a number of feature requests. We’re always excited to hear from you. If you’re interested in one of the features above or have something to suggest, please reach out!
Start your 30-day free trial
Helping You Make Great Things…Better.