PLM
Product Build Management with Aligni
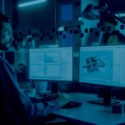
When Aligni manages builds, all the relevant details needed to make sure production has the parts they need are managed in a single location. This information can be shared easily with purchasing, inventory, quality, and manufacturing departments. Aligni build management provides a single source of truth for the entire production operation.
That localization also provides the company overarching management of part and material needs. This leads to more effective sourcing, scheduling, and oversight that can mean the difference between higher prices and production delays or more efficient, higher quality throughput.
The build management capabilities of Aligni offers several features that lead to benefits highly competitive manufacturers can’t ignore. Below is an overview of those benefits.
Centralized part information management
Aligni’s builds are the hub for part and material data. The system is designed to house all relevant information for each component that makes up a product’s bill of materials and saves the component’s details under a unique part number. Aligni makes it possible to collect per product part quantities, component specifications, quotes, vendor information and documentation. An Aligni build becomes the central information hub for the product build that departments like purchasing, engineering, inventory, and production can work from.
Detailed part availability visibility
Through the Aligni build process, manufacturers can allocate, reserve, and record consumption of parts in the firm’s inventory. The system can be used to model production needs and ready proactive measures to ensure smooth operation. Aligni can monitor inventory levels in the face of production usage and even alert purchasing to when parts need to be ordered.
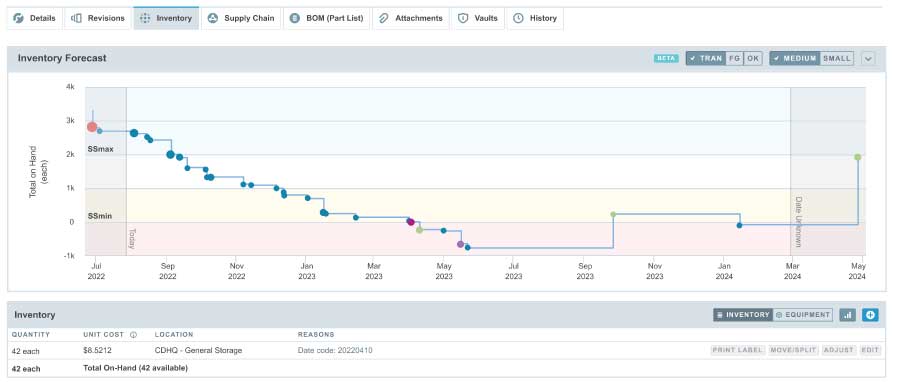
Manage inventory beyond a single build.
When all production orders are entered into Aligni, all of the company’s current and upcoming builds can be monitored and planned in one location. This provides both purchasing and production the ability to look long term at inventory needs, rather than being in a reactive state. Production is able to modify operation schedules to account for inventory on hand while purchasing can be more strategic about managing vendors. For the latter this means the opportunity to negotiate better pricing and more useful delivery times. For the former, it reduces out of stock surprises, downtime, or excessive changeover events.
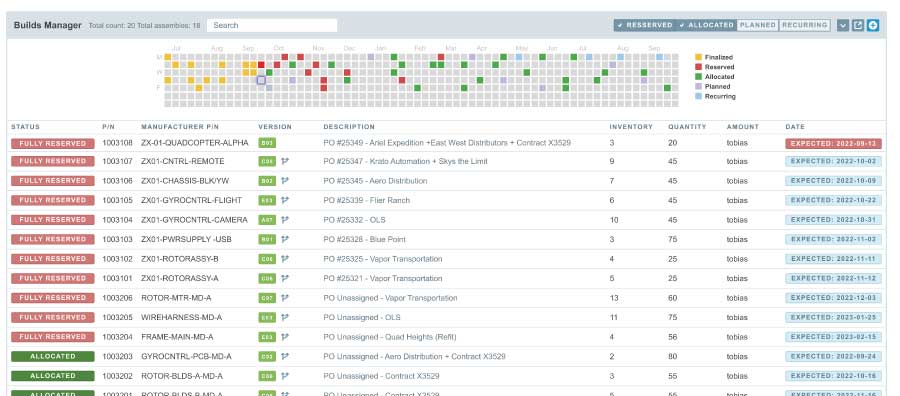
Explore what Aligni can do for your organization
Go Further
The above benefits are only a summary of the capabilities and tools Aligni provides to its users. Many firms discover further benefits once Aligni’s build management processes are adopted in their production operations.
If you’re ready to take production inventory management to the next level, it’s time to sign up for Aligni today and get these benefits and more for your plant floor.
Start your 30-day free trial
Helping You Make Great Things…Better.