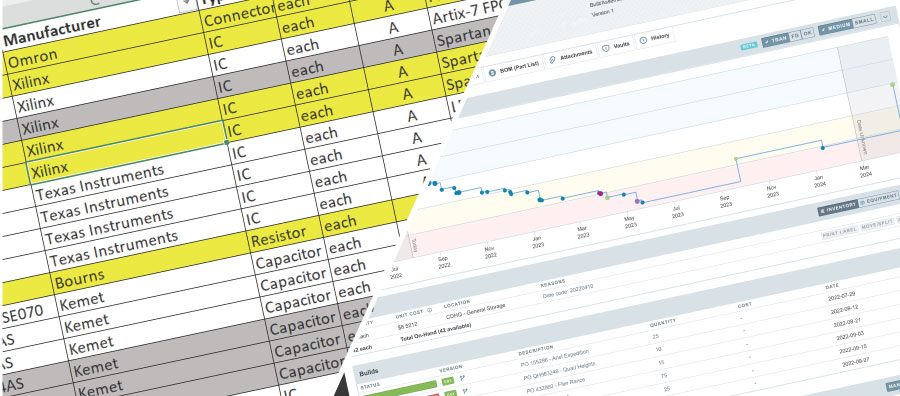
Relying on spreadsheets to manage inventory and production needs seems like a quick and easy solution in the beginning. Afterall, spreadsheets are low-cost, reliable commodity tools that are broadly familiar to nearly anyone working with computers. When manufacturing operations move from the simple to the complex, spreadsheets show their threads.
Spreadsheets aren’t designed to scale in the new dimensions and hierarchies needed for proper management of several build configurations. Adding more functionality to the file also contributes to conflicts and eventually corruption if the file gets unwieldy enough.
Where Spreadsheets Break Down
It’s great to have everything in one place, but a spreadsheet is not designed to manage vendor interactions. The buying process can be a high-touch operation where negotiations are managed in email. Translating those machinations into a spreadsheet is cumbersome at best, or it’s ignored altogether.
Sharing the spreadsheet between people and departments becomes a cumbersome process. Eventually, the file loses its accuracy as updates happen less frequently. Or worse, the file gets copied and propagated across the organization and no department is working off of the correct information.
If buyers are forced into managing purchasing through means not designed for the process, they may move towards processes that fit more neatly into a spreadsheet. This may mean online wholesalers or catalog vendors where prices are taken, not negotiated. This prevents the company from getting better prices, terms, or even the best part for the product found by establishing vendor relationships.
Finally, the “tool”’s use as an archive of currently or previously ordered parts is severely limited by the simple search functionality available in the spreadsheet software. When the file becomes large enough, the ability to find alternate parts becomes impaired. Eventually, engineers and buyers start sourcing new parts. More parts and more duplicate parts adds further to the file’s complexity.
The Right Tool for the Job
This is where Material Resource Planning (MRP) systems come in. MRP software like Aligni is purpose built to help manufacturers plan and manage the entire production process. The software handles everything from the procurement of raw materials to the delivery of finished goods. MRP systems plan and control the ordering, movement, and storing of materials and components necessary to meet customer demand. These systems track and schedule the materials and components needed to complete a manufacturing project, taking into account lead times, lead times, inventory levels, and other factors.
Migrating to an MRP system to manage the supply chain against production needs instead of ad-hoc, inconsistent, difficult-to-maintain spreadsheet processes has many advantages, especially for high mix operations managing highly specified or just a large amount of parts.
Tracking Material for Current Jobs
Going from spreadsheets – even specially designed, in-house versions – to a material resource planning system can provide manufacturers with far better visibility into inventory changes. With purpose-built user interfaces and access from a variety of departments, information can be easily updated and monitored.
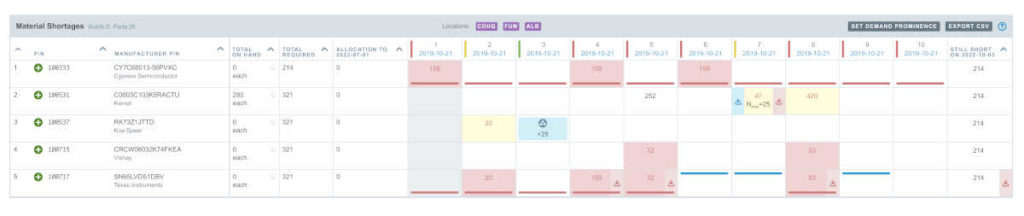
This visibility allows managers to view from one screen issues before they develop with current jobs. An MRP system can easily display how these issues will affect future materials needs. The software can do this because the data is saved in a database instead of a single file. That feature makes it easy to find and connect disparate data into actionable information.
Integrated Demand Estimation for Multiple Jobs
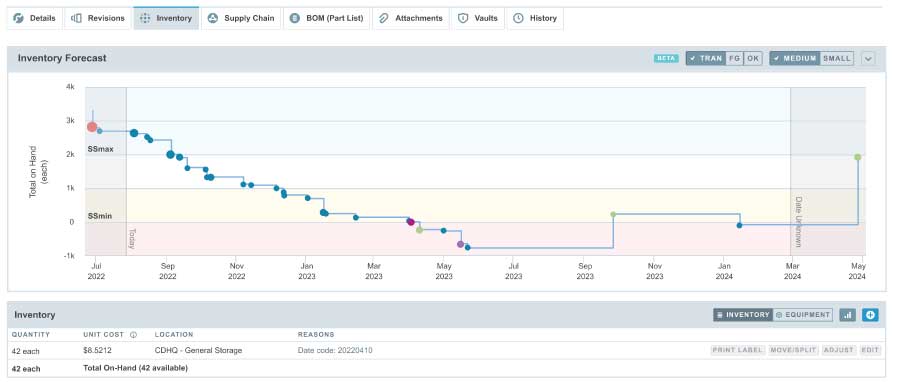
When the move to an MRP system happens, companies can get a lot more out of their data – especially when it’s all combined in the same system. With spreadsheets, typically the files are either set up to manage current and historical data or the files are built to analyze future possibilities. With an MRP system, both processes are combined in one system. That means it’s easier to use the wealth of prior performance to more accurately understand future needs.
Storing both historical data and future demand in a centralized database also makes it easy to manage a number of jobs and the potentialities of each over the course of successive orders. Viewing the combined effects of the jobs is easier to understand using an MRP system. Adding more jobs to manage is easy to do, as the database and the user interfaces are designed for the task and for expansion.
Collaboration with Other Departments Within the Firm
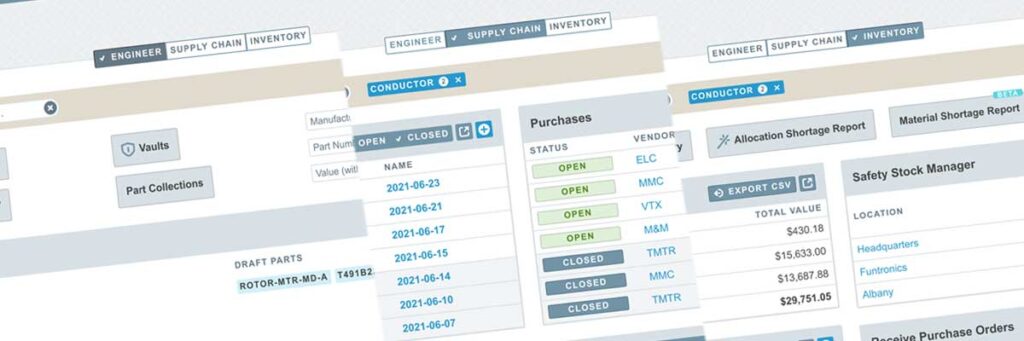
Using an application instead of a file brings other benefits to an organization. One of those is access. A database driven application like Aligni MRP is designed to provide several departments with the ability to monitor and update information as needed. Unlike home grown spreadsheets, each functional group doesn’t need to have training on how to operate the system. These access points are specifically designed to cater to the unique needs of each department instead of trying to satisfy the disparate needs of each group. This makes it easier and faster to manage and get value out of the system.
When every department has access to the same data set, it means all departments are working from the most current data available to the organization. No more work group information silos or waiting for update meetings – even for the purchasing process. Aligni MRP is designed to manage and operate on the buying process. All inventory information is available to everyone immediately.
If you’ve been in the trenches with spreadsheets, purpose-built MRP systems may seem like a luxury. When a company experiences the value a system can bring like the ones listed above, they wonder what took so long to migrate to a proper MRP system. Don’t be that company. Sign up online for Aligni MRP today and streamline your processes.
Start your 30-day free trial
Helping You Make Great Things…Better.