Engineering Change Orders (ECOs) are an important tool for manufacturers to track and report changes in product design, components, and production processes. In the overarching process of Engineering Change Management (ECM), ECOs and Engineering Change Requests (ECRs) work together. In doing so, they provide the structure necessary to maintain high part and product quality throughout the product development, manufacturing, and sourcing processes.
By themselves, ECOs provide a transparent and traceable system for documenting product design revisions and component changes. By issuing ECOs when changes take place, manufacturers can ensure their products remain compliant with the highest quality standards. ECOs also keeps engineers up-to-date with ever-evolving industry requirements.
ECOs in Use
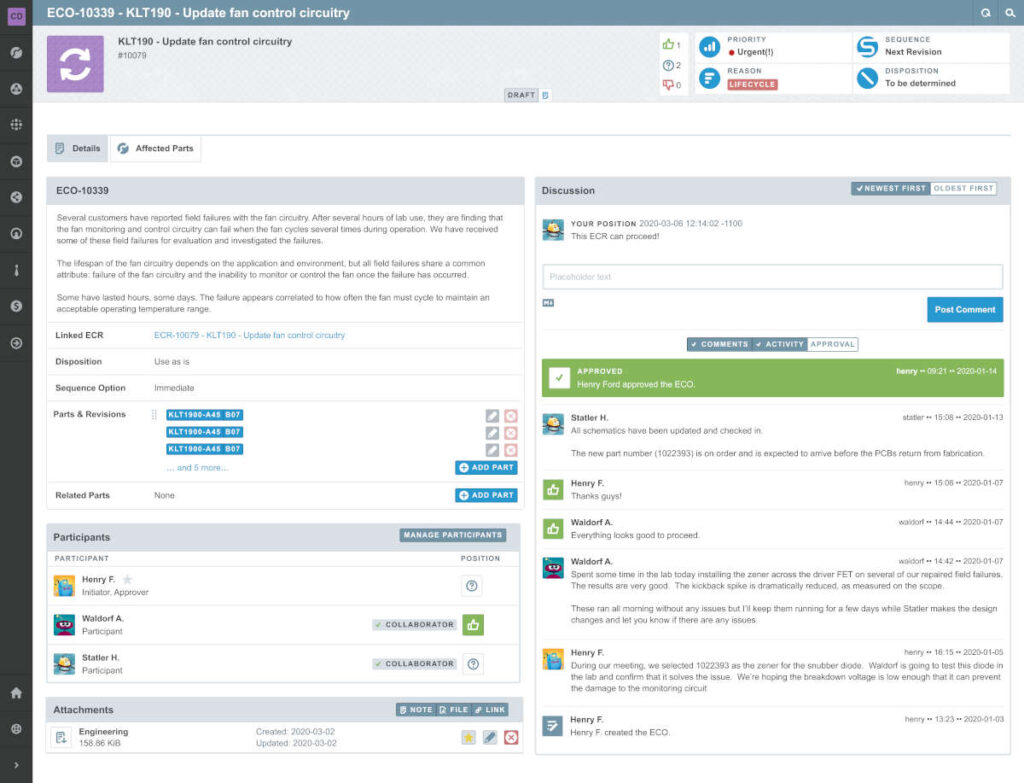
In a production setting, an Engineering Change Order is issued when a change has been proposed and approved in the engineering part of a manufacturing process. These changes may be due to quality issues, part availability situations, cost reductions, customer requirements, or other reasons. The ECO documents all changes between revisions of the product or component. Once an ECO is issued, specific areas of the business are notified including engineering, purchasing, and production departments. This allows manufacturers to trace back any discrepancies that may arise during inspections or testing. In addition, it can be used as a reference point for future improvement efforts.
ECOs also help ensure that quality remains high throughout the manufacturing process. It helps ensure existing products conform to predetermined specifications while continuing to improve product performance and quality in the face of supplier issues or part availability. They also provide clear communication between engineering and production departments about changes that need to be made. This connection helps prevent costly errors due to miscommunication.
By providing a transparent system for documenting and tracking changes, ECOs help manufacturers ensure that their products remain compliant with the highest quality standards. Moreover, these orders make it possible to add improvements to keep up with changing market requirements. ECOs are therefore essential tools for maintaining quality control at every stage of production. They also minimize risk by providing detailed records of modifications or improvements made in the design process.
Engineering Change Orders help minimize risk by providing detailed records of any modifications or improvements that have been implemented in the design process. Accordingly, they ensure all stakeholders in the manufacturing process are on the same page. As such, ECOs are essential tools for maintaining quality control at every stage of the production process.
Better Management through Software
Previously, these operations were classically instituted through paper processes. Now ECOs and ECRs have been digitalized into PLM and MRP systems like Aligni. Using PLM and MRP software helps eliminate human error in reporting and management. It also provides the ability to store and utilize the data created for extracting useful insights. By utilizing software-based engineering change order systems, manufacturers can more efficiently monitor the ECM process, regardless of the level of engineering and production complexity the company requires.
If you’re looking to get better control over part changes and quality issues on the shop floor, it’s time to check out what Aligni can do for your production operations. Sign up today!
Start your 30-day free trial
Helping You Make Great Things…Better.