Managing a manufacturing operation takes a lot of data, coordination and scheduling. Parts, prices, availability, and production capability have to interact seamlessly to get the maximum output out of a facility. While smaller operations can get by just with traditional office applications, larger, more complex operations manage too much to easily manage – or even fit – in a spreadsheet. These firms need purpose-built software, like MRP.
What is an MRP system?
A Material Requirements Planning (MRP) system for manufacturing automates and streamlines the management of production-related activities. It helps manufacturers effectively plan, schedule, and control the procurement and production of materials and components needed to meet customer demands. The MRP system, like Aligni MRP, uses data from various sources, such as sales forecasts, customer orders, inventory levels, and lead times, to help managers generate a comprehensive production plan.
In the MRP system, manufacturers create a Master Production Schedule (MPS) that outlines the quantities and timing of finished products to be produced. The system then breaks down the MPS into detailed material requirements by analyzing the Bill of Materials (BOM) for each product and considering any batch deviations specified. It calculates the net requirements for raw materials and components by considering the available inventory, scheduled receipts, and safety stock levels. The MRP system generates recommendations for purchase orders and production orders. This helps ensure the right materials are available at the right time to meet production schedules and customer demand. By reducing the complexity in managing these processes, MRP systems optimize production planning, minimize inventory costs, and improve overall operational efficiency for manufacturing companies.
How production planning done in an MRP system
When using an MRP system for performing production planning, nearly every aspect of the process is managed within the system. These aspects specifically involve determining what and how much to produce and the resources needed to produce them. The MRP system provides the ability to take into account various factors like customer demand, inventory levels, lead times, and production capacity. These systems add greater value through use of computer-based algorithms and calculations to streamline this planning process.
Here’s an overview of how production planning is typically done in an MRP system:
1. Creating the Master Production Schedule (MPS)
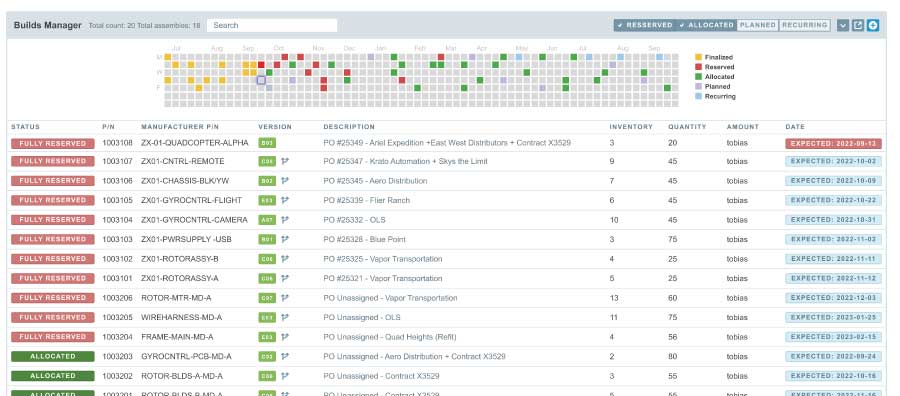
After compiling the relevant demand and resource information, the first step in MRP production planning is creating an MPS. This schedule is a detailed plan that specifies the quantity and timing of finished products to be produced over a specific period. The MPS is based on customer orders, sales forecasts, and other demand factors.
2. Preparing the Bill of Materials (BOM)
The next step is to prepare a Bill of Materials (BOM) for each finished product. The BOM lists all the components and raw materials required to manufacture a specific product, along with their quantities and relationships. The BOM serves as a foundation for calculating the material requirements.
3. Evaluating current inventory on-hand
The MRP system evaluates the current inventory levels of all materials and components required for production. It takes into account both on-hand quantities and scheduled receipts from suppliers.
4. Calculating Inventory Requirements
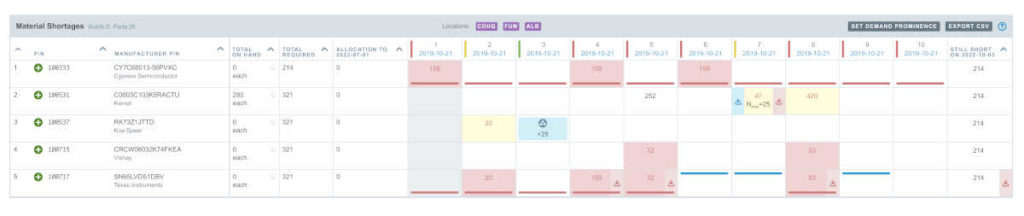
The MRP system then calculates the net requirements for each material and component needed for production. The net requirement is the difference between the required quantity for production (from the MPS and existing orders) and the available inventory.
5. Estimating material lead times
The lead time for each item is taken into account during production planning. Lead time refers to the time it takes to receive materials or components once they are ordered. It ensures that materials arrive on time for production, considering the required lead time and the timing of the production schedule.
6. Establishing safety stock quantities and reorder points
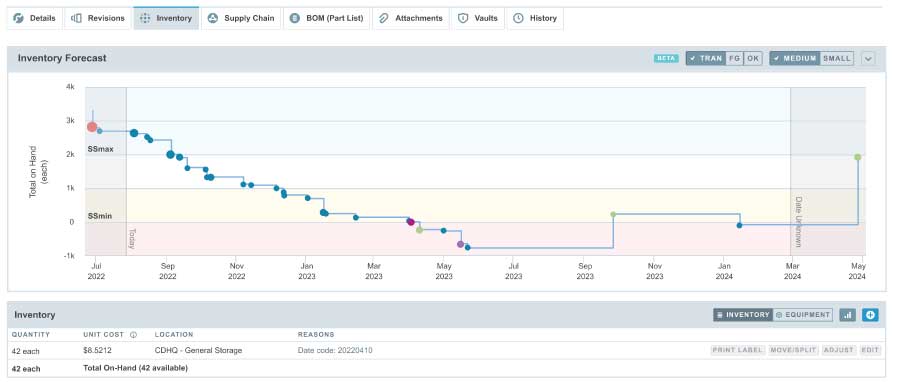
The MRP system also considers safety stock levels for critical items to handle any unexpected fluctuations in demand or supply disruptions. It calculates reorder points, indicating when to initiate the replenishment process for each material.
8. Factoring in capacity planning
MRP systems may integrate with Enterprise Resource Planning (ERP) systems to perform capacity planning. This involves evaluating the available production capacity and matching it with the production schedule to ensure that the production plan is feasible and does not overload resources.
9. Executing the plan and monitoring performance
Once the production plan is generated, it is executed by initiating production orders and procurement activities. Throughout the execution, the system monitors actual production and inventory levels to adjust the plan if necessary, taking into account any changes in demand or supply conditions.
Why use MRP systems for production planning?
Using a Material Requirements Planning (MRP) system for production planning offers several significant benefits for manufacturing companies. These systems enhance efficiency by automating and streamlining the production planning process. With real-time data integration and automated calculations, manufacturers can create accurate and detailed production schedules, ensuring that the right quantities of materials are available at the right time, minimizing production downtime and reducing the risk of stockouts or overstock situations.
Companies can use MRP systems to improve inventory management by optimizing material requirements. By taking into account factors like lead times, reorder points, and safety stock levels, manufacturers can maintain leaner inventories while still meeting customer demand and production schedules. This helps reduce holding costs associated with excessive inventory levels and frees up working capital for other investments. Additionally, the ability to forecast demand accurately and plan accordingly helps prevent stockouts, ensuring that customers receive their orders on time, leading to increased customer satisfaction and loyalty.
Better resource utilization and capacity planning can be easily achieved through the use of MRP systems. Manufacturers can assess the available production capacity and allocate resources efficiently based on the production plan. This helps prevent bottlenecks and enables better coordination between different departments. It also ensures resources are optimally utilized throughout the production process. MRP systems facilitate better coordination between production and procurement departments. This collaboration ensures materials and components are ordered in a timely manner to reduce lead times and improve overall production efficiency.
Bringing it all together
Production planning in an MRP system empowers manufacturers to make informed decisions, streamline their operations, and optimize their resources effectively. It leads to improved production efficiency, reduced costs, and enhanced customer satisfaction, all of which contribute to the long-term success and competitiveness of manufacturing companies.
Looking to get a better handle on your production planning processes? Then it’s time to investigate migrating to a material requirements planning system, like Aligni MRP today.