Inventory lead time in manufacturing refers to the time it takes for raw materials or components to be delivered and become available for use in production. It encompasses the entire process from initiating a purchase order or material requisition to the arrival of the materials at the manufacturing facility.
Inventory lead time is a critical factor in production planning and inventory management as it helps determine when to initiate procurement activities. This ensures a continual supply of materials for efficient production scheduling. It’s so critical that, for many manufacturing firms, trying to manage lead times with spreadsheets is too difficult to pursue. These companies turn to Material Requirements Planning (MRP) systems, like Aligni MRP to manage inventory time lines instead.
For a little background, an MRP system is a purpose-built software solution used to efficiently plan and manage the materials needed for production. It utilizes information such as bill of materials, inventory levels, and production schedules to calculate material requirements, generate purchase orders, and ensure timely availability of materials to meet production demands.
MRP does this through managing all relevant information within its item master database. This allows the system to not only store but easily access the large amounts of data generated to stay on top issues and find valuable insights. This is a major advantage over trying to accomplish the same through two-dimensional spreadsheets.
When it comes to lead time management MRP systems offer a number of key functions and benefits. We’ve listed the eight most important areas below.
1. Lead Time Calculation
MRP systems incorporate lead time information for each item in the inventory. This includes the time required to procure raw materials, manufacture or assemble the product, and deliver it to the customer. By capturing lead time data, make it easy for buyers to accurately estimate how long it takes to fulfill customer orders and plan accordingly.
2. Lead Time Variability Analysis
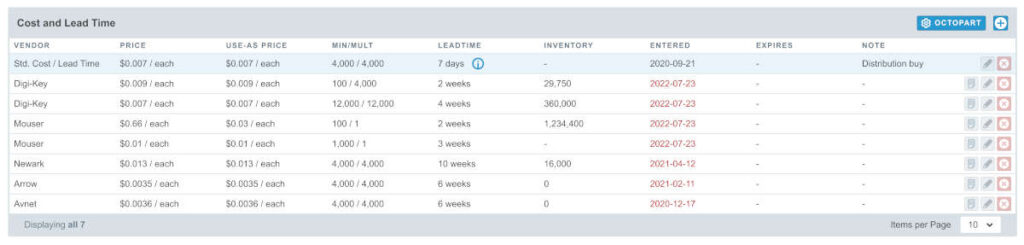
MRP systems provide the ability to analyze lead time variability by considering historical data, supplier performance, production capacity, and other relevant factors. By evaluating lead time variability, supply chain managers can help identify potential delays or uncertainties in the supply chain and take appropriate actions.
3. Replenishment Planning
MRP systems use lead time information to determine when to initiate replenishment orders. By considering lead times, MRP systems can calculate reorder points—the inventory level at which new orders should be placed—to ensure that stock is replenished in a timely manner, taking into account both demand and lead time.
4. Order Tracking and Visibility
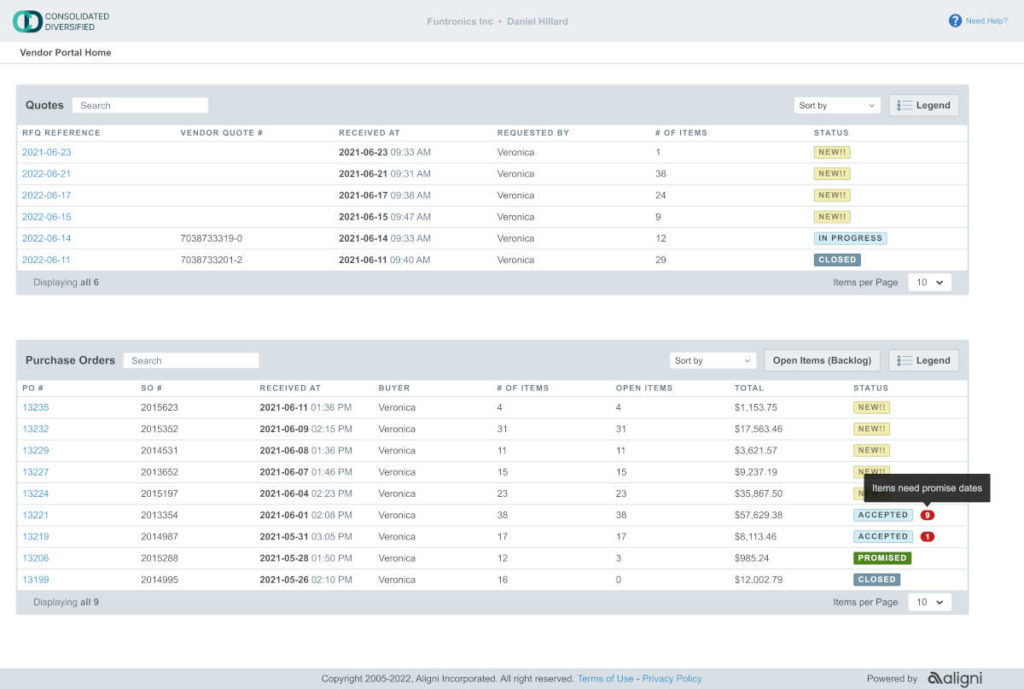
MRP systems can provide real-time visibility into the status of orders and their associated lead times. For example, Aligni MRP’s Vendor Portal provides a singular collection point for order information. This allows supply chain managers to track the progress of orders throughout the supply chain, monitor lead time performance, and take proactive measures to address any deviations or delays.
5. Supplier Management
Some MRP systems facilitate effective supplier management by capturing and analyzing lead time performance for different suppliers. Aligni MRP does this through its ActiveQuote system where current and historical purchasing information is stored for easy analysis.
This information helps supply chain managers evaluate supplier reliability, negotiate contracts, and make informed decisions about sourcing and supplier selection based on lead time considerations.
6. Demand Planning and Forecasting
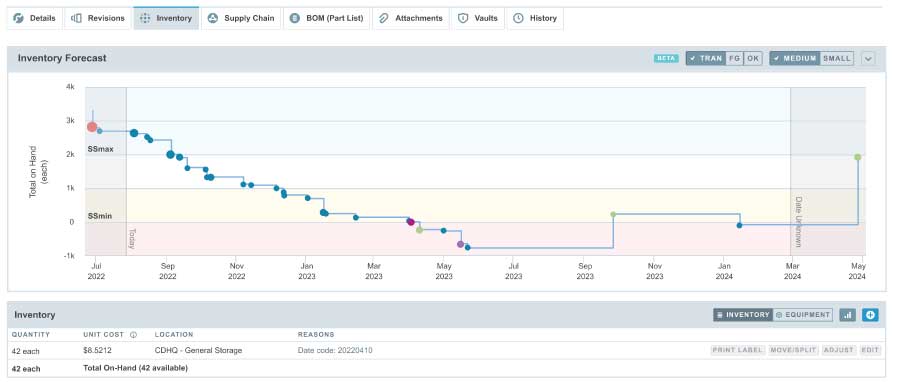
Many MRP systems integrate demand planning functions, allowing supply chain managers to align inventory lead times with anticipated demand. By incorporating demand forecasts, MRP systems enable better coordination between production schedules and lead time requirements, helping to avoid stockouts or excess inventory.
7. Simulation and Scenario Analysis
This capability enables supply chain managers to assess the sensitivity of their operations to lead time variations and make informed decisions based on different scenarios. MRP systems support simulation and scenario analysis to evaluate the impact of changes in lead times on inventory levels, production schedules, and customer service levels.
8. Continual Improvement
By providing comprehensive lead time data and performance metrics, MRP systems facilitate continual improvement efforts within the supply chain. Supply chain managers can use this data to identify bottlenecks, inefficiencies, or areas for optimization in lead time management, and implement corrective actions to enhance overall supply chain performance.
These functionalities help streamline operations, optimize inventory levels, reduce stockouts, and improve customer satisfaction. All are made easier through the use of Material Requirements Planning systems and their ability to manage large amounts of inventory data and make it easily accessible for supply chain managers.
If you’re swimming in inventory data and would like to turn that data into greater efficiency and reduced stockouts, it’s time to migrate to a purpose-built MRP system. It’s time to sign up online for Aligni MRP today.
Start your 30-day free trial
Helping You Make Great Things…Better.