Effectively keeping track of inventory is not something that only happens in real-time. It also needs to be done with an eye towards future needs. To properly understand what parts and materials are needed in future operations, the inventory tracking system needs to have the ability to consider customer demand and calculate a forecast for what will be needed to satisfy it.
Thinking in this integrated manner is one thing that sets apart efficient, proactive manufacturers from less efficient, reactive ones. Before we can look at how these systems work together, we need to understand how each works on its own.
Knowing the Processes
Inventory tracking for manufacturers is a process that involves systematic monitoring and management of raw materials, work-in-progress (WIP), and finished goods throughout the production cycle. The process begins with setting up and organizing the inventory management system, recording incoming materials, and creating a detailed Bill of Materials (BOM) for each product. The process continues with WIP tracking, providing real-time updates on production progress. It then continues with monitoring finished goods until shipment. Continual analysis of inventory data enables manufacturers to optimize their supply chain, maintain optimal stock levels, and meet customer demands efficiently.
Demand estimation for manufacturing is the process of analyzing current and historical sales data, market trends, and other relevant factors to predict future customer demand for manufactured products.
By using various forecasting techniques and data-driven methodologies, manufacturers can anticipate demand fluctuations, identify patterns, and make informed decisions about production levels, inventory management, and supply chain optimization. Accurate demand estimation enables manufacturers to align production schedules with customer needs, maintain optimal inventory levels, and enhance operational efficiency to meet market demands effectively.
How Do Inventory Tracking and Demand Estimation Work Together?
Between these two descriptions, it’s not difficult to see why demand estimation and inventory tracking are designed to work together in a manufacturing environment. They partner to optimize inventory levels and ensure businesses meet customer demands efficiently. Here’s how demand estimation and inventory tracking complement each other:
Tighter Reorder Point Calculation
The reorder point represents the inventory level at which new stock needs to be ordered to avoid stockouts. Demand estimation helps forecast when this reorder point will be reached, enabling proactive reordering and preventing inventory shortages. Businesses can calculate the reorder point for each item when demand estimation and inventory tracking are combined.
More Effective Safety Stock Management
Safety stock acts as a buffer to handle unexpected spikes in demand or delays in the supply chain, ensuring customers are not left waiting for products. Demand estimation helps identify potential demand variability or uncertainties. Inventory tracking can help identify fluctuations on the supply side by analyzing historical supply chain data. Businesses can combine this information to determine the appropriate level of safety stock.
Greater Production Planning Efficiency
Integrating demand estimation with inventory tracking allows businesses to plan production more efficiently. By knowing the expected demand, manufacturers can align production schedules with customer needs. This minimizes excess production and ensures products are available when needed.
Data-Driven Decision Making
When forecasted customer demand is combined with historical production data, manufacturers can do a far better job of estimating materials needed without running out of parts or over-purchasing to cover phantom needs. Instead of guesswork, managers can make informed decisions about inventory levels, purchasing, and production based on accurate forecasts combined with real-time inventory data and a rich understanding of the true needs of the shop floor.
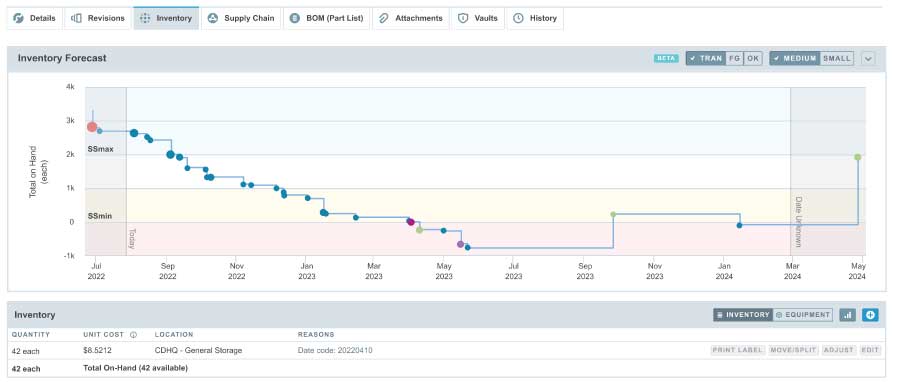
Sharper Inventory Optimization
By integrating demand estimation data into its inventory tracking process, businesses can optimize their inventory levels. Balancing demand forecasts, safety stock requirements, and inventory lead times, they can reduce carrying costs while ensuring sufficient stock to meet customer demands.
Avoiding Stockouts and Overstocking
Having adequate stock on hand prevents production downtime due to material stockouts. On the other hand, avoiding overstocking helps reduce holding costs and potential losses due to unsold inventory. The synergy between demand estimation and inventory tracking helps businesses strike that perfect balance in inventory management where production runs efficiently, and cash flow isn’t locked up in warehouses.
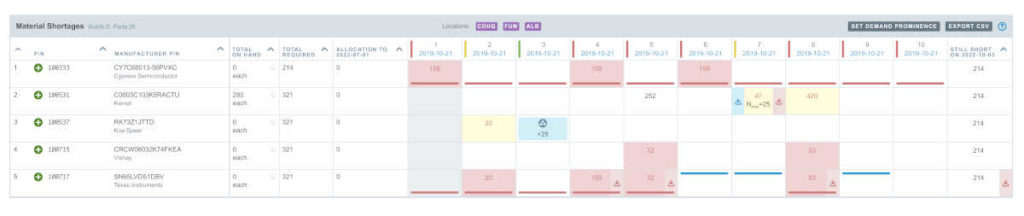
Managing with the Right Software
For efficient manufacturing operations, it’s almost required to make sure demand estimation and inventory tracking work hand-in-glove to support effective inventory management. The integration of these two processes is essential for businesses to achieve efficient supply chain management and meet customer expectations effectively.
While some companies may still try to manage both processes with home grown spreadsheets, the amount of data necessary to manage both processes efficiently makes a purpose built software solution a necessity. There is simply too much information to manage within a spreadsheet and too much specialized programming needed within it to get near the value the integration could provide. Secondly, a spreadsheet’s ability to share that data across work groups is awkward and limited, at best.
The better solution is to migrate to a Materials Requirements Planning (MRP) system. This software is purpose-built to handle the integration of both processes. MRP systems like Aligni have built in functionality that can estimate future demand without the need for complex machinations of spreadsheet formulas or macros.They also make it easy to increase participation between the departments. This collaboration and depth of data handling is needed to see the results from inventory planning and demand estimation working together.
If it’s time to get more effective at inventory management by connecting the dots between inventory tracking and demand estimation, then it’s time to make a move to a proper system. It’s time to sign up online for Aligni MRP today.
Start your 30-day free trial
Helping You Make Great Things…Better.