Inventory analysis is a process manufacturing companies use to ensure efficient use of resources and to minimize waste. The process involves examining various aspects of inventory such as quantity, location, value, age, and production demand patterns. It also looks at supply chain processes. Companies use this information to develop better inventory management processes that reduce carrying costs, stockouts, overstocking, and other issues.
While there may be manual aspects to the process, the bulk of the analysis happens within software designed to manage a company’s parts and materials inventory and ordering process. The common systems used are Enterprise Resource Planning (ERP) and Material Resource Planning (MRP) software. The latter is found more commonly in small and medium-sized businesses. These systems are adept at managing the large quantities of data that are created within the manufacturing process, as well as exploring the rich historical data available.
The Inventory Analysis Process
A company’s inventory process is highly dependent on how the products are produced and what quality and performance metrics the products need to maintain. Below is a generalized series of steps involved in the inventory analysis process for manufacturing operations:
1. Collect Inventory Data
The first step in inventory analysis is to gather data on inventory levels, locations, and values. This data can be collected through physical counts, automated tracking systems, or a combination of both.
2. Categorize Inventory
Inventory should be categorized by product type, value, age, and location. This will help identify which items are slow-moving, high-value, or in excess.
3. Determine Inventory Turnover
Inventory turnover measures the number of times inventory is sold and replaced within a specific time period. This metric is useful in identifying slow-moving or obsolete inventory.
4. Analyze Demand Patterns
Analyzing demand patterns can help identify trends in customer demand, which can inform production and inventory management decisions.
5. Calculate Inventory Carrying Costs
Inventory carrying costs include the cost of holding inventory, such as storage, insurance, and handling costs. Understanding these costs can help identify areas where inventory can be reduced.
6. Determine Safety Stock Levels
Safety stock levels are the amount of inventory kept on hand to meet unexpected increases in demand or production delays. This level should be based on demand variability and lead time.
7. Identify Inventory Optimization Opportunities
Based on the analysis of inventory data, opportunities for optimization can be identified. This may include reducing excess inventory, adjusting production schedules, or improving demand forecasting.
Scheduling Inventory Analysis Processes
The fast-paced nature of component lifecycles, complex supply chains, and the need for precise production timing drives organizations to this greater inventory oversight. To maintain optimal inventory levels, minimize waste, and ensure uninterrupted operations, a structured and consistent schedule of analytical activities is required. The following schedule outlines a practical cadence—spanning weekly, monthly, quarterly, and annual tasks—to help manufacturers proactively manage inventory, identify potential risks, and align stock with production and market demand.
Weekly Activities
Day | Activity | Purpose |
Monday | Review stock levels of A-items | Ensure availability of high-value, critical components |
Tuesday | Update demand forecasts (short-term) | Align procurement with sales/production updates |
Wednesday | Evaluate safety stock and reorder points | Adjust based on recent demand or supply fluctuations |
Thursday | Cycle count (select inventory categories) | Validate system accuracy through sample counts |
Friday | Check WIP levels and aging | Prevent WIP bottlenecks and identify delays |
Monthly Activities
Week | Activity | Purpose |
1st week | Full ABC analysis update | Reflect any changes in component consumption/value |
2nd week | Lead time review with suppliers | Identify any risks or shifts in procurement timelines |
3rd week | Analyze inventory turnover | Assess efficiency and inform future stocking strategies |
4th week | Identify slow-moving/obsolete items | Plan liquidation, repurposing, or write-offs |
Quarterly Activities
Quarter | Activity | Purpose |
Every Q | Full physical inventory audit | Ensure financial reporting accuracy and detect shrinkage |
Every Q | BOM (Bill of Materials) review | Check for component substitutions or redesigns |
Every Q | System review (ERP/MRP tuning) | Optimize rules, alerts, and master data accuracy |
Annual Activities
Month | Activity | Purpose |
Q4 (or fiscal year-end) | Strategic supplier performance review | Evaluate delivery, quality, and lead time compliance |
Q4 | Inventory policy review and budget planning | Set new reorder thresholds, safety stocks, and budget |
Q4 | Obsolescence risk planning | Forecast risk of component EOL (End-of-Life) parts |
Comparing Data to Established Metrics
Once they have the data, companies establish baseline practices and metrics for inventory analysis to ensure consistency, efficiency, and performance tracking across their operations. These baselines define standard procedures—such as ABC classification, cycle counting, and forecasting methods—and set measurable targets for key performance indicators.
To effectively monitor and improve inventory performance, electronics manufacturers track a set of key metrics that serve as both operational benchmarks and decision-making tools. For example, the inventory turnover ratio measures how quickly inventory is sold or used, helping identify excess stock or sluggish demand. Cycle count accuracy, often tracked as a percentage, reflects the alignment between physical inventory and system records, ensuring reliability in planning and reporting. The stockout rate reveals how often inventory shortages disrupt production or sales, prompting corrective actions in replenishment strategies. Carrying cost of inventory quantifies the financial burden of holding stock—such as warehousing, insurance, and depreciation—guiding decisions around optimal inventory levels. Finally, the obsolescence rate highlights the proportion of inventory that becomes outdated or unusable, which is especially critical in electronics where components can quickly lose relevance.
These metrics provide a data-driven foundation for evaluating performance, identifying inefficiencies, and driving continuous improvement in inventory management. By doing this, organizations create a reliable benchmark for managing inventory proactively, identifying issues early, and driving continuous improvement. Baselines also enable better decision-making, support training and accountability, and are often integrated into MRP or ERP systems to automate monitoring and enforce best practices—as well as to handle the large quantities of data that go into these metrics.
The Right Tools for the Job
Inventory analysis in electronics manufacturing presents a unique set of challenges that often exceed the capabilities of manual processes or basic tools like spreadsheets. One of the primary complexities lies in managing detailed, multi-level Bills of Materials (BOMs), which can include hundreds or thousands of components per product. Tracking these dependencies and ensuring accurate material availability requires automation—something that purpose-built MRP (Material Requirements Planning) systems handle efficiently. Demand volatility further complicates matters, as market shifts, customer behavior, and frequent design changes can render forecasts obsolete. MRP systems like Aligni integrate forecasting data to dynamically adjust procurement and inventory plans in real time.
Long and unpredictable lead times, especially for critical components like semiconductors, also make manual planning risky. MRP software manages these variables by incorporating supplier lead times into safety stock and reorder point calculations. It also addresses the risk of component obsolescence by flagging End-of-Life (EOL) items and integrating with lifecycle and supplier databases. Real-time visibility into inventory levels is crucial, and without it, organizations risk costly stockouts or overstock situations. MRP systems provide accurate, location-specific inventory data, enabling better decision-making and just-in-time procurement.

Another critical function is synchronizing material procurement with production schedules. Misalignment here can result in idle workstations, delayed shipments, and wasted labor. MRP systems ensure material availability is closely tied to production timelines, while also tracking Work-in-Progress (WIP) inventory in real time. Compliance and traceability requirements, especially in industries with strict regulatory oversight, add yet another layer of complexity. MRP solutions enable batch tracking, part traceability, and audit-ready reporting to support quality and regulatory standards. As electronics manufacturers scale and product lines grow, the need for integrated, automated, and scalable systems becomes unavoidable. MRP software offers a central solution by linking inventory, procurement, production, and financial data, making it essential for efficient and accurate inventory analysis in modern electronics manufacturing.
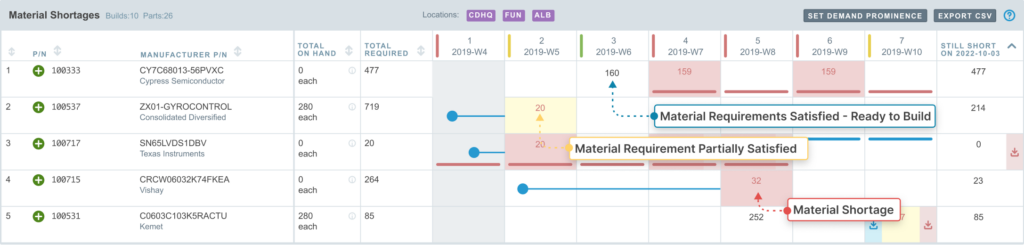
Summing It All Up
As can be seen in the steps above, inventory analysis is a vital process for manufacturing companies looking to optimize their inventory management practices and improve efficiency and profitability. With so much data available, it all but requires the use of dedicated software to perform.
By analyzing inventory data, companies can make more informed decisions about their inventory levels, production schedules, and supply chain relationships. The insights stemming from the process typically results in significant cost savings and increased competitiveness.
Looking to put inventory information to work in the search for greater efficiency and lower costs? Time to sign up for Aligni MRP today!
Start your 30-day free trial
Helping You Make Great Things…Better.