When it comes to production efficiency, many manufacturers will tell you the one thing they cannot change is how much time they have – there’s only 24 hours in a day. What they can change is what can be accomplished in that time. The goal is to pack as much productivity as possible into the hours they have. While firms can buy more and faster machines or hire more people, the simplest – and most difficult – thing is to make sure there are no lags in production. Typically, those lags come from either breakdowns or part shortages.
Manufacturers must prevent material shortages to maintain production continuity, meet customer demands, and ensure business profitability. Material shortages can lead to production delays, increased lead times, and missed delivery deadlines, resulting in dissatisfied customers and potential loss of business. Moreover, production stoppages and rush orders to address shortages can incur extra costs, negatively impacting the bottom line.
Metrics to watch to reduce material shortages
Managing a production operation’s supply chain can be complex. Getting the right information about the current situation and forecasting future needs is central to effective management. This process boils down to metrics. Manufacturers need to track various key metrics and data points to effectively reduce material shortages and optimize their supply chain. We’ve listed some of the more essential elements to monitor:
1. Current Inventory Levels
Keep track of your current inventory levels for each material or component. This includes raw materials, work-in-progress (WIP), and finished goods.
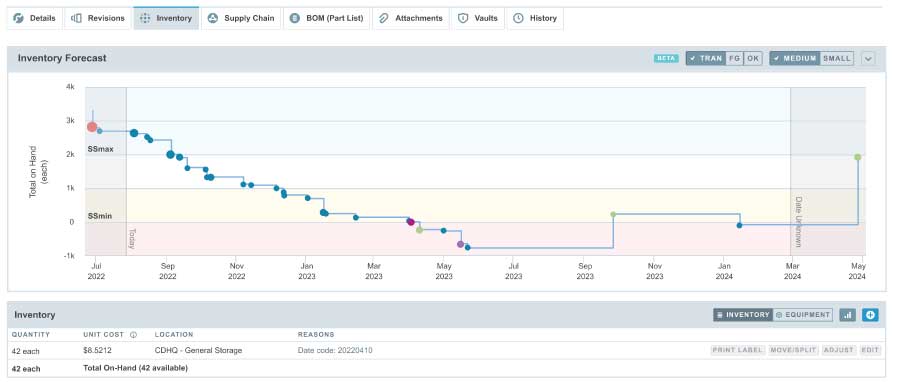
2. Demand Forecasts
Monitor and update demand forecasts regularly to align production and procurement with customer requirements.
3. Part and Material Lead Times
Understand the time it takes to receive each material or component, including the elapsed time from ordering to delivery.
4. Supplier Performance
Assess supplier performance by tracking metrics like on-time delivery rates, quality, and lead time reliability. This is necessary as it factors into lead times and actual quantities that need to be ordered for specific batch sizes.
5. Safety Stock Quantities
Keep tabs on safety stock levels for critical materials to ensure buffer stock is maintained to handle unexpected fluctuations in demand or supply disruptions.
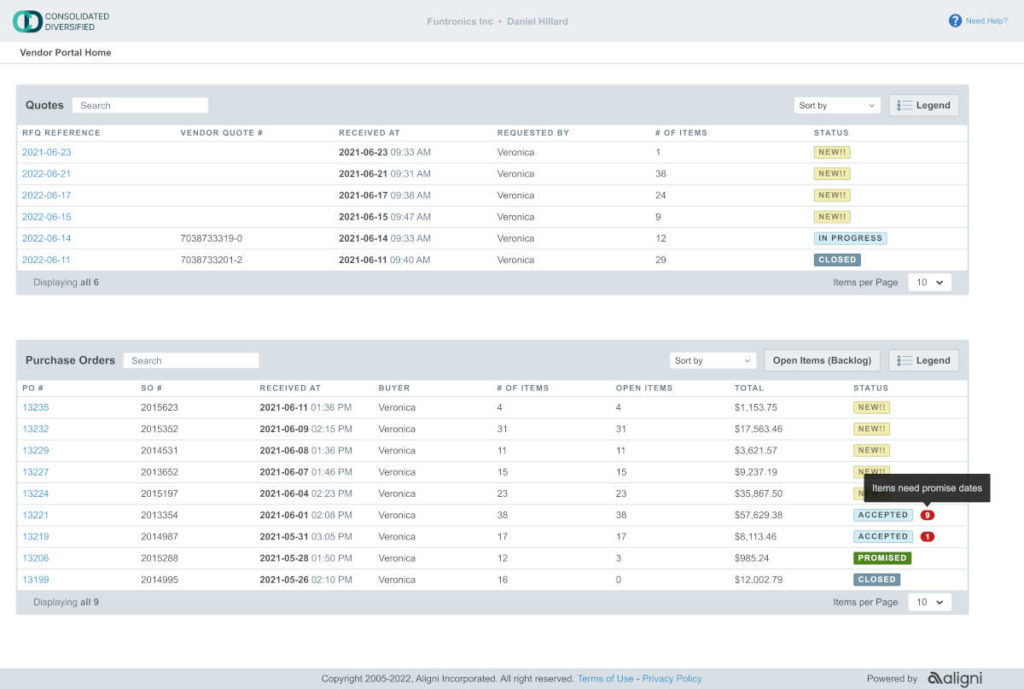
6. Order Status
Track the status of open purchase orders and production orders to ensure they are progressing as planned. This ensures the company can make changes quick enough to production scheduling to offset missed or stretched delivery dates. Maintain a list of alternate parts to substitute when specified parts are in short supply.
7. Internal Production Schedules
Monitor production schedules to ensure they align with demand forecasts and material availability.
8. Quality Control Issues
Keep records of quality control data to identify any recurring issues that may lead to material shortages due to rejected or substandard materials. Having these records linked to production processes and parts makes it easy to make adjustments to the buying process to offset issues.
9. Obsolete Inventory
Identify and track obsolete or slow-moving inventory to minimize tied-up capital and storage space.
10. Material Traceability
Implement systems to trace materials and components back to their source, which can help identify the root causes of shortages or quality issues.
11. Supplier Relationships
Maintaining a database of supplier contacts, agreements, and communication records helps facilitate effective collaboration. Set up a list of preferred vendors who have proven performance in meeting deadlines and quality metrics.
12. Market Trends
Stay informed about industry and market trends that may impact material availability and demand. This can be done through analyzing historical pricing and availability for estimations of future situations.
13. Production Efficiency
Monitor production efficiency metrics to identify areas where process improvements could reduce material waste. It’s also important to better understand part usage quantities to more efficiently order and retain materials for production.
14. Cost Analysis
Regularly review the cost structure of materials and components to identify cost-saving opportunities and potential alternatives.
15. Regulatory Compliance
Stay up to date with regulatory requirements related to materials and components, ensuring compliance to avoid disruptions.
16. Supplier Diversification
Track the progress of efforts to diversify your supplier base to reduce dependency on a single source.
17. Continuous Improvement
Regularly review and analyze historical data to identify trends and areas for improvement in your supply chain processes.
By tracking these key elements, manufacturers can gain better visibility into their supply chain, proactively address material shortages, and make informed decisions to optimize their operations.
Tracking metrics more effectively with MRP systems
Effective data management and analysis are required for success in this endeavor, but the above list turns out to be a lot of data to track. For most firms, it’s too much data to manage just through spreadsheets. These firms turn to software designed to track these metrics while storing the large amounts of data for deeper analysis. The software of choice is usually a Material Requirements Planning (MRP) system for small and medium sized companies.
Manufacturers can effectively manage key metrics using an MRP system as a central hub for their supply chain and production operations. With a system like Aligni MRP, manufacturers can seamlessly track inventory levels, demand forecasts, lead times, and supplier performance. The system automatically calculates material requirements based on demand forecasts, taking into account lead times, safety stock, and production schedules. It generates purchase orders, ensuring materials are ordered in a timely manner to prevent shortages. By monitoring the status of these orders and maintaining real-time visibility into inventory levels, manufacturers can proactively address material shortages and optimize inventory management.
Furthermore, an MRP system facilitates data-driven decision-making by providing comprehensive reports and analytics on metrics like supplier performance, cost analysis, and quality control. It helps manufacturers identify trends and areas for improvement, enabling continuous process optimization. With integrated risk assessment and collaboration tools, manufacturers can mitigate supply chain risks and foster better communication with suppliers.
Bringing it all together
Efficient material management not only reduces operational disruptions but also enhances overall supply chain resilience, helping manufacturers remain competitive and responsive in a dynamic marketplace. Doing this with an MRP system streamlines operations, enhances efficiency, and minimizes material shortages by offering a holistic view of the supply chain while automating many of the data processes involved in materials management.
Looking to plug those production gaps by minimizing stockouts? Time to invest in an MRP system that can help you manage inventory data to find insights and be more proactive. It’s time to sign up for Aligni MRP.
Start your 30-day free trial
Helping You Make Great Things…Better.