The longer a product is manufactured, the more common it is for the parts and materials that go into the item to change over time. In fact, for some industries, it’s more common for parts to change more often than others. The reason for these changes can come from a variety of factors: the originally specified parts are no longer available, performance requirements change, vendors change or something else entirely.
Whatever the reason, manufacturers and supply chain managers need to keep track of the variations to make sure production runs smoothly with the correct parts. That means a system needs to be put in place to accurately differentiate major changes from minor ones.
Revisions or Versions: the difference is important
Having a robust strategy to distinguish between part versions and revisions in inventory management is essential for accurate operations and streamlined processes. Clear differentiation ensures precise inventory control, preventing errors and confusion that can lead to stockouts or overstock situations. This accuracy facilitates effective production planning, allowing the right materials to be available when needed and avoiding confusion. Moreover, an effective strategy enhances traceability, supporting quality control, audits, and compliance with regulations. Efficient communication across departments, optimized inventory costs, and smoother transitions for new part versions are additional benefits. A well-structured strategy promotes accuracy, efficiency, and compliance in inventory management, positively impacting customer satisfaction and the bottom line.
A comprehensive and well-executed part identification strategy reduces wasted resources by preventing the use of incorrect parts in production, conserving raw materials, labor hours, and energy. It also supports continuous improvement initiatives by providing a solid foundation for analyzing historical data and identifying areas for optimization. This strategy ensures proper supplier management, allowing effective communication about changes and ensuring the supply of correct part versions. By establishing a framework for accurate part delineation, businesses can meet customer expectations, reduce operational risks, and foster a more successful and compliant inventory management process.
The distinction between part versions and part revisions
In manufacturing, both part revisions and part versions refer to changes made to a specific component or assembly used in the production of a product. However, each term represents different types of modifications. Just as a company tracks and documents changes to its own product and communicates these changes to customers, it will also track and document changes to the underlying components for internal reference. A revision to a part is more of an incidental change to the item. Understanding their distinctions is crucial for effective inventory management, production planning, and quality control. Below, we go into more depth on how these are different:
Part Revisions
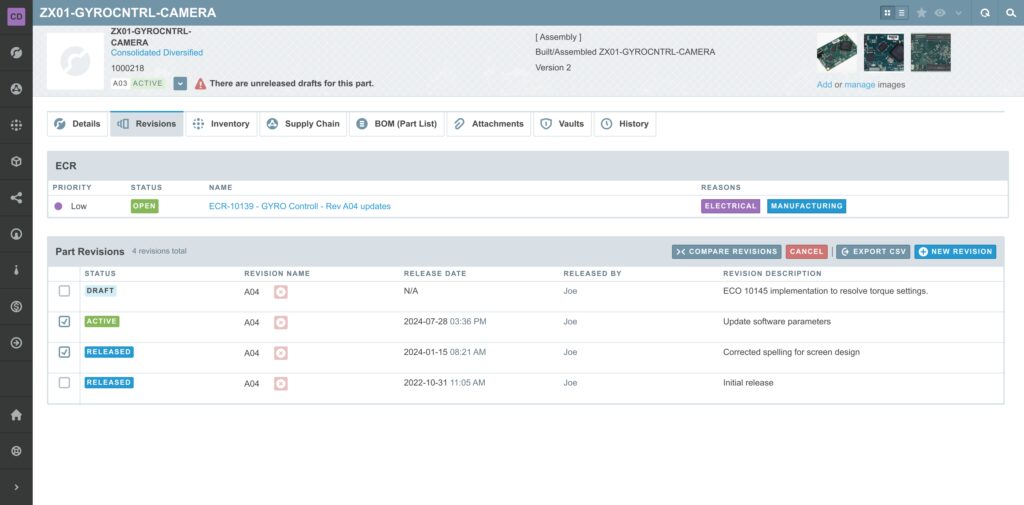
A part revision typically indicates a change made to an existing component or part that does not alter its fundamental form, function, or compatibility with the original design. Part revisions are often minor updates or improvements meant to address issues, enhance performance, or meet specific requirements without requiring significant changes to the overall product. These revisions might include adjustments to tolerances, material substitutions, minor design modifications, or corrections to manufacturing defects. The primary goal of part revisions is to maintain compatibility with existing products and processes while improving the part’s quality, efficiency, or reliability. Each part revision typically receives an incremental revision letter (e.g., Rev A, Rev B) to track and document the changes.
Part Versions
Part versions, on the other hand, represent more significant changes to a component or part that can impact the overall design, function, or compatibility of the part within the product or assembly. A part version denotes a distinct iteration of the part that may introduce substantial alterations, enhancements, or new features. Part versions often result from major design changes, the introduction of new technology, or the adaptation of the part for different applications. When a new part version is introduced, it may require updates to the product’s design, manufacturing processes, and even the Bill of Materials (BOM) to accommodate the changes. Part versions are commonly identified by numerical designations (e.g., Version 1, Version 2) and are more likely to result in the creation of entirely new part numbers to differentiate them from previous versions.
In summary, part revisions involve minor modifications to existing parts to improve quality or functionality while maintaining compatibility, typically denoted by revision letters. Part versions represent significant changes to a component or part, often requiring updates to the product’s design and manufacturing processes, and are designated by version numbers.
Effectively Managing part versions and revisions with an MRP
Managing part versions and part revisions in a Material Requirements Planning (MRP) system is a task that cannot be taken lightly. It involves careful planning and execution to ensure accurate production processes and smooth operations. It also requires team buy-in and continuous oversight to make sure the process and the conventions are followed. Here are some specific guidelines to follow:
1. Use Standard Naming Conventions
Define a standard naming convention for part versions and revisions. This could include using version numbers (e.g., v1, v2) and revision letters (e.g., A, B) in a consistent format that’s easy to understand.
2. Practice Version Control
Implement a version control system within the MRP system to track changes to parts over time. This ensures that the system maintains a record of all versions and revisions.
3. Keep Clear Documentation
Maintain easy to understand and detailed documentation for each part version and revision. Include information such as the reason for the change, description of the change, date of change, and personnel responsible for the change.
4. Institute a Change Approval Process
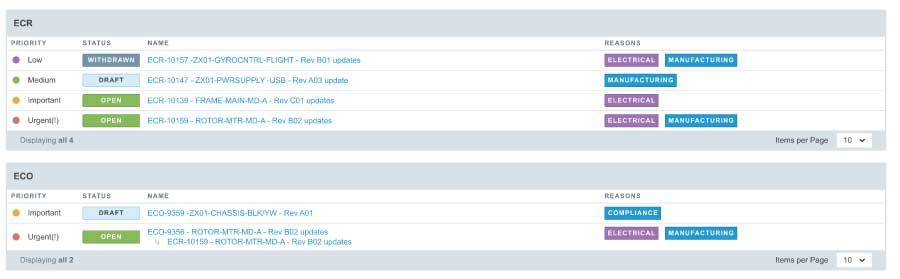
Establish a formal change approval process that involves relevant stakeholders, such as engineering, production, and quality control. Changes should be reviewed, approved, and documented before implementation. Most MRP systems, like Aligni MRP, include Engineering Change Management (ECM) functionality that provides processes like these.
5. Bill of Materials (BOM) Updates
Whenever a part version or revision changes, update the BOM accordingly. This ensures that production planning remains accurate and reflects the most current information.
6. Track Traceability
Maintain traceability by linking each part version or revision to its associated documentation, such as drawings, specifications, and testing results. This ensures that historical data is readily accessible. An MRP system is designed to hold information like this in a centralized location within its item master database.
7. Use Effective Communication
Communicate changes to all relevant departments and individuals in a timely manner. This prevents confusion, reduces the risk of errors, and ensures everyone is on the same page. Most companies who employ MRP systems use it as the hub for communicating changes across departments, as the system is designed to be accessed by relevant parties within the organization.
8. Maintain Supplier Collaboration
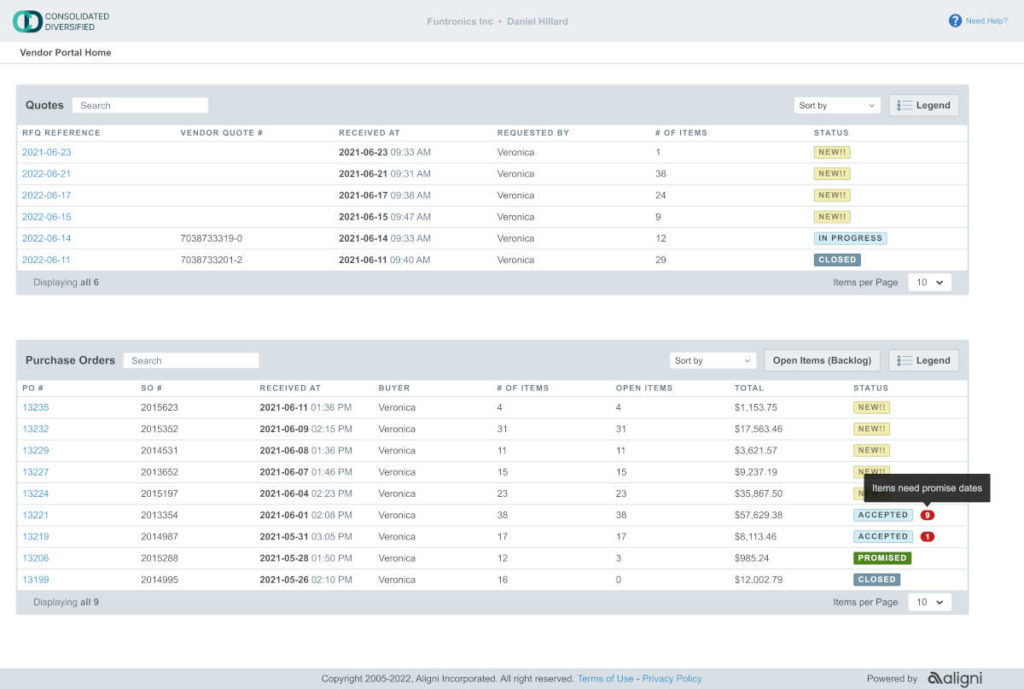
If changes to parts affect suppliers, communicate with them about the changes and any potential impact on their processes or deliveries. Aligni’s MRP solution has unique functionality that integrates into the purchasing process, making the collaboration with vendors much more streamlined.
9. Testing and Validation
Before implementing changes, conduct thorough testing and validation to ensure that the new part versions or revisions meet the required standards and function as intended.
10. Keep a Rollback Plan
Have a contingency plan in place to revert to previous part versions or revisions if unforeseen issues arise during or after implementation.
11. Data Integrity and Security
Implement measures to ensure data integrity and security within the MRP system. This includes access controls, data backups, and regular audits. Cloud-based MRP systems like Aligni also provide data backups offsite for further data security.
12. Provide Training and Knowledge Sharing
Provide training to employees involved in managing part versions and revisions. Additionally, encourage knowledge sharing between departments to promote better understanding of changes.
13. Practice Continuous Improvement
Regularly assess the effectiveness of your part version and revision management processes. Identify areas for improvement and implement changes accordingly.
14. Historical Archive
Maintain a historical archive of older part versions and revisions. MRP systems like Aligni have a leg up on spreadsheet-based systems as their item master database backend provides far better access to older data, making analysis much easier. This helps with referencing past designs and troubleshooting issues that may arise with legacy products.
15. Auditing and Compliance
Regularly audit your part version and revision management processes to ensure they align with industry standards and regulatory requirements.
Why firms manage part variations in MRP
The guidelines above seem like a lot of process to manage. It’s certainly too much to manage through a selection of spreadsheets and email. That’s why most firms manage these within an MRP system. These systems, like Aligni MRP, are based on an item master database. That makes them ideal for handling the large amounts of data and the data’s interconnections between products and projects. This more efficient data handling manifests itself in a variety of benefits to manufacturers.
MRP systems ensure precise inventory management by accurately tracking part versions and revisions, preventing stockouts, and optimizing inventory costs. This approach enables effective production planning, allowing the MRP system to incorporate the correct materials and quantities based on specific versions or revisions. This leads to streamlined production scheduling and reduced errors. Additionally, the enhanced traceability facilitated by proper version and revision management supports quality control, regulatory compliance, and product consistency.
Managing part versions and revisions in an MRP fosters efficient change management processes. The system documents changes, enabling clear review, approval, and implementation, reducing the likelihood of errors or disruptions during production. Collaboration across departments improves significantly, with engineering, production, procurement, and other teams working together more effectively due to shared, up-to-date information, minimizing misunderstandings and ensuring alignment with the latest changes.
Lastly, the MRP system’s historical data, driven by managed part versions and revisions, supports better data-driven decision-making. This information aids in identifying trends, assessing change impacts, and making informed choices for continuous improvement initiatives. Smooth transitions from older part versions to new ones are ensured, preventing production disruptions, phasing out older parts efficiently, and maintaining production continuity.
Ultimately, these benefits collectively lead to operational efficiency, cost optimization, customer satisfaction, and a more agile and responsive manufacturing process. If you’re looking to get these benefits, then it’s time to migrate to Aligni MRP!
Start your 30-day free trial
Helping You Make Great Things…Better.