When you’re designing and building products, accurately sharing what needs to go into the product is highly important – especially when the firm relies on sourced parts in the product’s assembly.
In order to make sure the right information is shared, the Bill of Materials (BOM) management process needs to be integrated with a variety of other production management processes. That’s why many firms turn to Material Requirements Planning (MRP) systems to manage their BOMs and parts lists.
Managing BOMs within MRP systems offers manufacturers a streamlined and efficient approach to integrating product parts lists into production and supply chain operations. This interconnection enables accurate material requirements planning, reducing the risk of stockouts and overstocking. It can also lead to optimized resource utilization and lower production costs.
With precise BOM management provided through a proper MRP system like Aligni, organizations can ensure product quality, meet delivery deadlines, and adapt to changing market demands swiftly, all while fostering collaboration with suppliers and improving decision-making processes. In a single sentence, managing BOMs in MRP systems enhances production efficiency, cost control, and overall competitiveness in the market.
Looking at the benefits of BOM and MRP integration
Managing Bills of Materials in a Material Requirements Planning system offers several significant benefits for manufacturing organizations. We’ve listed fourteen of the most important below:
1. Accurate Production Planning
MRP systems use BOMs to calculate precise material requirements, ensuring that the right components and quantities are available when needed for production. Making sure the MRP is using the most current information through integrated part lists minimizes the risk of stockouts or overstocking.
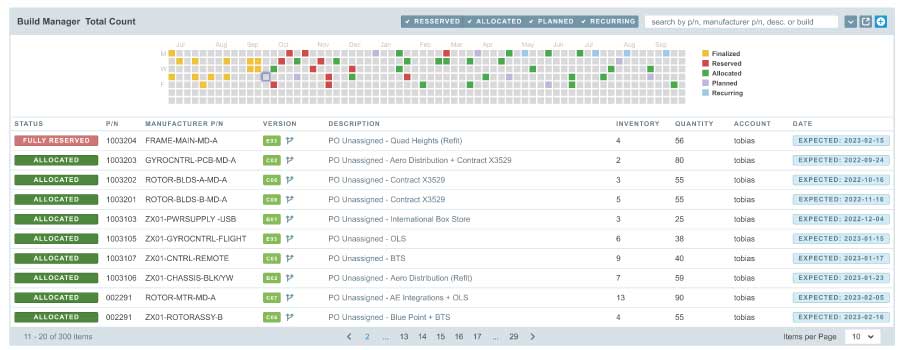
2. Better Inventory Control
MRP systems use the integrated product BOMs to help maintain optimal inventory levels by using them to generate purchase orders or production orders based on actual demand and lead times. This reduces carrying costs associated with excess inventory and makes sure the right quantity of parts are ordered.
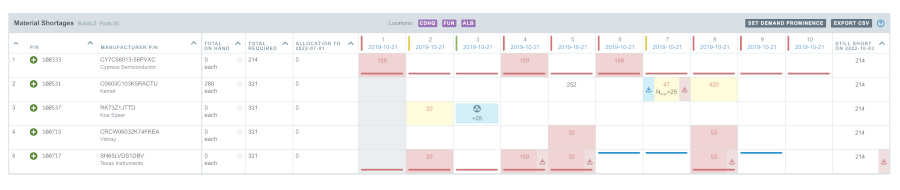
3. Minimizing Production Delays
BOMs enable MRP systems to identify potential bottlenecks or shortages in the production process early by connecting the product’s material needs to stock on hand and sales demand. This allows organizations to take proactive measures to prevent delays and meet delivery deadlines.
4. Reduced Waste
Accurate BOM management minimizes the risk of producing excess or incorrect components, reducing material waste and associated costs, as the part list data is directly connected to production activities and purchasing operations, rather than being stored in spreadsheets that may or may not be shared in a timely manner with these groups.
5. Improved Quality Control
By ensuring that the correct components are used in the production process, BOM management contributes to improved product quality and reliability. When the BOM is stored within the MRP system, this allows quality control personnel to view the most current information on a product’s makeup.
6. Effective Change Management
It’s common to find firms managing engineering change management (ECM) operations within MRP systems. That means organizations can efficiently manage changes to product designs or manufacturing processes and see those changes reflected in the integrated BOMs. This facilitates faster adaptation to market demands and regulatory requirements.
7. Improved Supplier Collaboration
BOMs linked to supplier information in the MRP system enable better collaboration and communication with suppliers. While some MRP systems make this information available to the company’s buyers, advanced systems like Aligni MRP have the capability to directly interact with suppliers to further reduce timelines. This ensures timely deliveries of components and helps supply chain managers negotiate favorable terms.
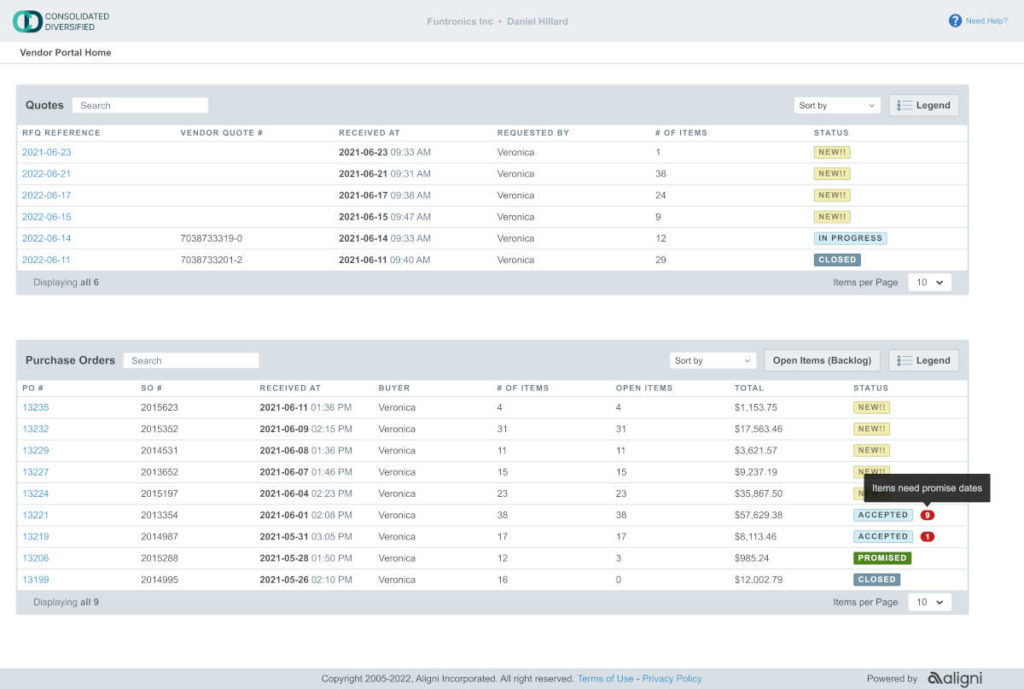
8. Enhanced Productivity
The management of BOM-related tasks in an MRP system reduces manual efforts associated with making sure downstream processes and groups are informed and using up-to-date information. This allows employees to focus on more value-added activities, such as process improvement or innovation instead of double-checking data and calling unnecessary meetings.
9. Better Decision-Making
Access to real-time data from the MRP system, including BOMs, empowers decision-makers with accurate and timely information for strategic planning and resource allocation. It allows production managers to better fit operations to parts on hand and provides supply chain managers better understanding of what’s needed on the shop floor before issues arise.
10. Reduced Costs
By optimizing inventory levels to only the parts required and adjusting quickly to changes in product makeup, integrated BOMs reduce production delays and improve resource utilization, The combined operations lead to significant cost savings.
11. Compliance and Traceability
BOM management helps organizations maintain compliance with industry regulations by ensuring that the right materials and components are used. It also improves traceability in the case of recalls or quality issues.
12. Integrated Capacity Planning
MRP systems use BOMs to calculate capacity requirements for each component and sub-assembly. Managing the BOM in the MRP means this part list data is already integrated into the planning aspects of the company. This helps manufacturers allocate production resources efficiently.
13. Streamlined Interdepartmental Communication
BOMs serve as a common reference point for different departments within an organization, streamlining communication and promoting cross-functional collaboration.
14. Higher Customer Satisfaction
Meeting delivery timelines and consistently delivering quality products, facilitated by effective BOM management, leads to higher customer satisfaction and loyalty.
Bringing it all together
Managing BOMs in an MRP system is an invaluable practice for manufacturing organizations that want to enhance their operational efficiency, reduce costs, improve product quality, and stay competitive in the market. It streamlines processes and helps organizations respond quickly to changing market dynamics and customer demands.
The key to getting the most out of this interconnection is to make sure the MRP system the company is using can provide the level of integration necessary to see these benefits manifest in a productive manner. If you’re looking to connect the dots between managing your products’ BOMs and your manufacturing processes, it’s time to migrate to Aligni MRP today!
Start your 30-day free trial
Helping You Make Great Things…Better.