Material Resource Planning (MRP) is a software-based inventory control and production planning system that helps manufacturers determine the materials they need to produce a product, schedule production runs, and track inventory levels. Inventory planning is an important component of what MRP systems provide to manufacturers.
In MRP systems, inventory planning works by employing customer demand data, production capacities and parts and material needs to determine the optimal inventory levels for each raw material and finished product. This involves analyzing historical sales data, lead times, and using demand forecasting techniques to predict future demand. The system then calculates the reorder point for each item. This is the inventory level at which a new order should be placed to ensure that the inventory does not fall below the desired level.
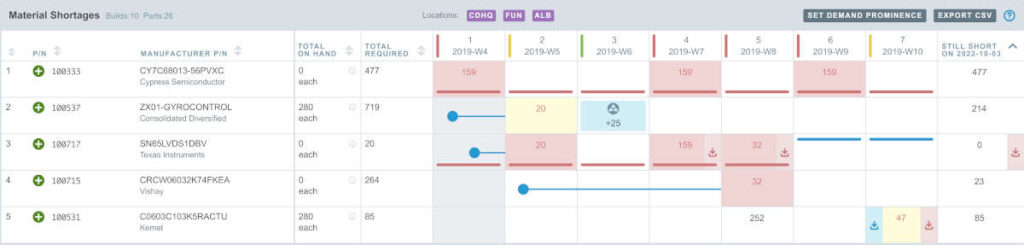
Once the reorder point has been calculated, an MRP system like Aligni generates purchase orders for raw materials and other inputs as needed. The system takes into account the lead time for each item, which is the time it takes for the supplier to deliver the item after an order has been placed. By factoring in the lead time, the MRP system ensures that the inventory levels will be replenished in time to meet customer demand.
The material resource planning system also tracks inventory levels in real-time and generates alerts when inventory levels fall below the reorder point. This ensures that manufacturers can quickly respond to changes in demand and avoid stockouts.
In addition to inventory planning, MRP systems can also help manufacturers plan and schedule production runs, track work-in-progress, and manage production capacity. By integrating inventory planning with these other functions, MRP systems provide small and medium-sized manufacturers with a comprehensive tool for managing their production operations and optimizing their inventory levels.
Benefits of Doing Inventory Planning with MRP
There are several arguments for doing inventory planning within an MRP system. Some of theses include:
1. Improved Inventory Control
By using MRP systems for inventory planning, manufacturers can gain greater control over their inventory levels. This can help them optimize inventory levels, reduce the risk of stockouts, and avoid overstocking.
2. Better Demand Forecasting
MRP systems use historical sales data and demand forecasting techniques to predict future demand for products. This can help manufacturers better anticipate customer demand and plan production accordingly.
3. Streamlined Production Scheduling
By integrating inventory planning with production scheduling, MRP systems can help manufacturers optimize production runs and minimize downtime. This can improve efficiency and reduce production costs.
4. Reduced Lead Times
MRP systems take into account the lead time for each item, which is the time it takes for the supplier to deliver the item after an order has been placed. By factoring in the lead time, manufacturers can ensure that inventory levels will be replenished in time to meet customer demand.
5. Improved Supplier Relationships
By using MRP systems for inventory planning, manufacturers can provide suppliers with more accurate and timely information about their inventory needs. This can help build stronger relationships with suppliers and improve the reliability of the supply chain.
Overall, doing inventory planning within an MRP system can help manufacturers optimize their inventory levels, improve production scheduling, and reduce lead times. By improving inventory control and demand forecasting, MRP systems can help manufacturers improve efficiency and reduce costs, while also improving customer service and building stronger relationships with suppliers.
Looking to get a better handle on inventory? Sign up for Aligni MRP today!
Start your 30-day free trial
Helping You Make Great Things…Better.