Keeping quality where it needs to be during production requires a lot of effort and planning. The process includes setting quality parameters before production, monitoring during manufacturing, and analyzing stored quality data to evaluate performance.
Performing these measures well requires software built for the tasks outlined above. Spreadsheets just won’t cut it. That’s why Material Resource Planning (MRP) systems like Aligni MRP play a crucial role in managing manufacturing quality in highly efficient small and medium sized manufacturing firms. MRP software provides the tools and functionalities to monitor, control, and improve the quality of products throughout the manufacturing process without drowning in data. With its integrated item master database, the software oversees information such as product specifications, material certifications, quality best practices, and testing data much better than two-dimensional spreadsheets.
While it’s also used to help manage quality control aspects, a system like Aligni MRP is known most as a software-based solution used to efficiently plan and manage the materials needed for production. The system’s core functions include streamlining demand forecasting, BOMs, inventory levels, and supply chain operations. Managing all these aspects in one system helps ensure timely availability of materials to meet production demands, as well as connecting production data with testing outcomes to find greater insights.
When it comes to quality, here’s how MRP systems specifically contribute to manufacturing quality management:
Managing Quality Control Parameters
MRP systems can act as a Quality Management System (QMS) and store quality control parameters such as inspection criteria, acceptance levels, and quality standards. These parameters are added into the system to ensure that manufacturing processes and finished products meet the required quality specifications. These test processes and their results are tied to the parts, products, manufacturing operations, and orders.
Inspection Planning and Scheduling
To ensure that inspections are performed at the right time and at the appropriate checkpoints, MRP systems facilitate the planning and scheduling of inspections and quality control activities. These systems can generate inspection orders or work orders with specific instructions for quality checks at various stages of the manufacturing process.
Defect Tracking and Non-conformance Management
MRP systems enable the tracking and management of defects and non-conformances with sorting and binning processes built in. When a quality issue is identified during the manufacturing process or during inspections, the system can capture the details of the non-conformance, including the affected product, location, and nature of the defect. This allows for proper investigation, documentation, and implementation of corrective actions.
Material and Inventory Management
MRP systems help ensure that only approved and qualified materials are used in manufacturing. The system can maintain a list of approved suppliers, manage material specifications, and track material certifications. This helps prevent the use of non-conforming materials and ensures that the right materials are available at the right time from trusted vendors.
Engineering Change Management
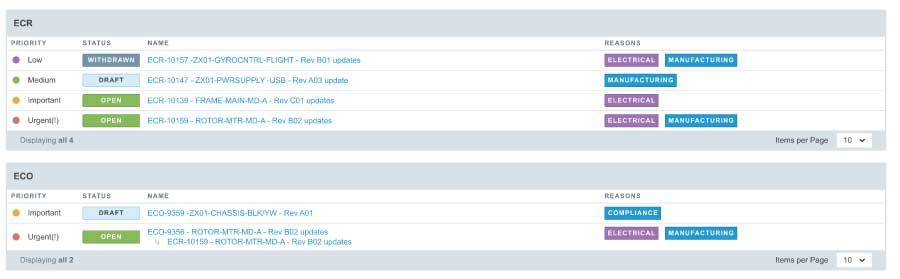
When there needs to be changes made to the makeup of a product, the ECM process makes sure the right changes are made and the correct people are notified. MRP systems, like Aligni, have integrated ECR and ECO capabilities that not only track changes but keep the people who need to know abreast of issues as they develop. This collaborative approach makes sure changes happen quickly and are documented as needed.
Bringing it all together
By incorporating these features and functionalities, MRP systems help manufacturers monitor and manage manufacturing quality, improve process control, reduce defects, and enhance overall product quality. They provide a structured approach to quality management and support continuous improvement efforts throughout the manufacturing lifecycle by increasing collaboration between the departments within a manufacturing organization.
Ready to move past spreadsheets in managing your manufacturing processes? It’s time to bring materials management, production planning and quality control together in one application. Time to sign up for Aligni MRP today.
Start your 30-day free trial
Helping You Make Great Things…Better.