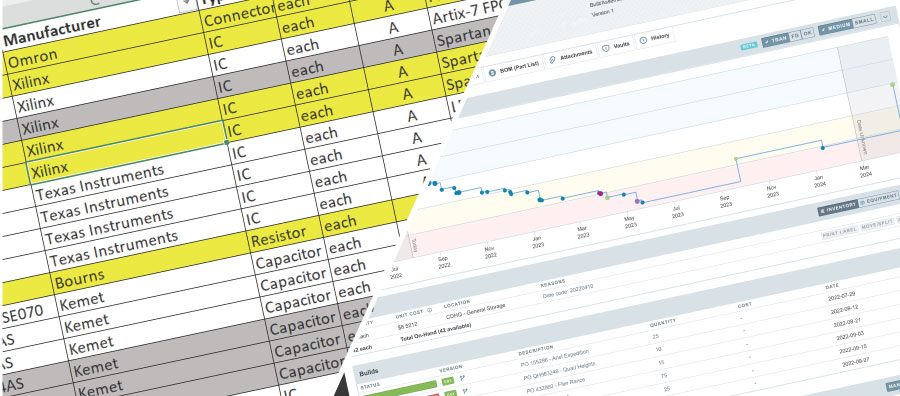
So you’re considering moving away from spreadsheets to a purpose-built system to manage production and supply chain operations and you’re wondering what this process might look like. At Aligni, we’ve helped hundreds of firms make the jump. We’ve seen this process many times and have put together some basic information to start you on your path to MRP success. This information should help you ask the right questions, corral the necessary data, and craft an individual plan for your organization that helps ensure a successful migration.
What data needs to be migrated into an MRP system for manufacturing?
Migration starts with the data – the most important aspect of the switch. When migrating to a Material Requirements Planning (MRP) system for manufacturing, several types of data must be transferred to ensure the system operates effectively and provides accurate information for production planning, inventory management, and other related functions. The specific data to be migrated may vary based on the organization’s processes, industry, and the features of the MRP system being implemented. However, here are the key categories of data that are typically migrated into an MRP system for manufacturing:
1. Item Master Data
This includes information about each item or product that the organization manufactures, purchases, or sells. It encompasses details such as item codes, descriptions, unit of measure, item classification, and product specifications.
2. Bill of Materials (BOM)
The BOM is a critical component of an MRP system. It specifies the components, raw materials, and sub-assemblies required to produce a finished product. Accurate BOM data is essential for generating material requirements and production schedules.
3. Warehouse and Location Data
Data related to warehouse layouts, bin locations, and storage capacities can be useful for optimizing inventory storage and management within the MRP system.
4. Inventory Levels
The MRP system needs to know the current inventory levels of all items in stock. This includes both finished goods and raw materials. Accurate inventory data ensures that the system can generate appropriate replenishment orders and avoid stockouts.
5. Supplier Data
Information about suppliers, including contact details, lead times, pricing, and terms of purchase, needs to be migrated. This helps the MRP system manage procurement processes, generate purchase orders, and optimize supplier relationships.
6. Customer Orders and Forecasts
Historical customer order data and demand forecasts are essential for generating accurate demand plans. This data helps the MRP system predict future demand and align production accordingly.
7. Production Orders and Work Orders
If the organization has ongoing or historical production orders, these records should be migrated. Work orders, which specify the tasks and resources required for production, are crucial for scheduling and resource allocation.
8. Quote and Lead Time Data
Information about lead times for both internal processes (e.g., production lead times) and external processes (e.g., supplier lead times) should be migrated. Accurate lead time data helps the MRP system calculate reorder points and safety stock.
9. Quality Control and Inspection Data
If the organization has quality control processes or inspection points within the production process, relevant data about quality standards, inspections, and testing can be important for ensuring product quality.
10. Historical Sales and Production Data
While not always necessary, having historical data on sales, production, and inventory levels can be valuable for trend analysis, forecasting accuracy, and benchmarking within the MRP system.
It’s important to work closely with the MRP system vendor and set up an internal implementation team to define the specific data requirements for the migration and ensure data accuracy. Plan for any data transformation or cleanup needed to align the existing data with the new system’s structure – as you’ll see below, the migration process will typically happen while your firm is continuing to make parts and save production data. Proper data migration is essential for the success of the MRP system implementation.
A sample timeline for migrating to an MRP
Once the data is ready to go or a plan is in place to copy the information, it’s time to consider the stages in making the transition happen. Below is a general outline for the steps in the timeline to migrating to an MRP system from a spreadsheet-based system:
1. Assessment and Planning
- Assess the current spreadsheet-based system.
- Identify pain points and areas for improvement.
- Create a project team and set objectives for the migration.
- Duration: 2-4 weeks
2. Research and Selection
- Research MRP systems that align with organization needs.
- Evaluate vendors and request demos.
- Select the most suitable MRP system based on criteria.
- Duration: 4-6 weeks
3. Data Preparation
- Cleanse and format data from existing spreadsheets.
- Organize relevant information for migration.
- Ensure data accuracy and consistency.
- Duration: 2-4 weeks
4. Training and Familiarization
- Provide training for employees on the MRP system.
- Ensure understanding of system features and functionalities.
- Conduct practice exercises for hands-on experience.
- Duration: 2-4 weeks
5. Pilot Testing
- Implement the MRP system on a limited scale for testing.
- Choose a specific product line or area for testing.
- Gather feedback from users and make necessary adjustments.
- Duration: 4-6 weeks
6. Full Implementation
- Migrate all data and processes to the MRP system.
- Establish necessary integrations with other systems.
- Roll out the MRP system across the organization.
- Duration: 4-12 weeks
7. Post-Implementation Review and Optimization
- Conduct a post-implementation review to assess effectiveness.
- Identify areas for further optimization.
- Monitor KPIs related to inventory management and efficiency.
- Continuously refine and improve the MRP system.
- Duration: Ongoing
Be aware, this outline is a generalized version of the steps needed to migrate. The actual timeline may vary depending on the organization’s specific needs, size, and complexity of the implementation. Engaging with experts and your MRP vendor can help ensure a successful and efficient migration process.
What issues might come up migrating from a spreadsheet system to an MRP system?
Migrating from a spreadsheet-based system to a Material Requirements Planning (MRP) system can be a complex process, and various issues may arise during the transition. Being aware of potential challenges allows organizations to plan and mitigate them effectively. While this is by no means exhaustive, here are some common issues that might come up during the migration:
1. Data Compatibility and Migration
One of the significant challenges is ensuring that the data from the spreadsheet-based system is compatible and can be accurately migrated to the MRP system. Data formats, structures, and conventions may differ between the two systems, leading to data loss, corruption, or inconsistencies. Migrating historical data accurately is critical for continuity and historical analysis.
2. User Resistance and Training Gaps
Employees who are accustomed to the spreadsheet system may resist the change and be reluctant to adopt the new MRP system. Inadequate training and unfamiliarity with the new system can hinder user adoption and productivity. Proper training and ongoing support are essential to ensure a smooth transition and user acceptance.
3. System Integration
Integrating the MRP system with other existing enterprise systems, such as accounting, ERP, or CRM, can be challenging. Data synchronization, API compatibility, and workflow alignment must be carefully addressed to avoid disruptions to existing processes.
4. Customization and Configuration
Configuring the MRP system to suit the specific needs of the organization may require customization. Balancing customization with the standard features of the MRP system is essential to avoid complexities, increased costs, and potential future compatibility issues.
5. Downtime and Business Continuity
During the migration, there may be a period of downtime or reduced efficiency as employees adjust to the new system. Proper planning for business continuity and data backup is crucial to minimize the impact on operations.
6. Cost and Budget Management
Migrating to an MRP system involves costs such as software licenses, hardware, training, and implementation. Managing the budget effectively and ensuring that the benefits of the MRP system justify the investment is essential.
7. Quality Assurance and Testing
Thorough testing is necessary to identify and resolve issues or bugs in the MRP system. Inadequate testing can lead to operational disruptions and compromise data integrity.
8. Vendor Support and Reliability
Choosing a reliable MRP system vendor with excellent customer support is crucial. If the vendor lacks support or fails to meet the organization’s needs, it can lead to difficulties in resolving issues and getting the necessary assistance during and after the migration.
9. Change Management
Implementing a new MRP system involves significant changes in processes and workflows. Proper change management practices are necessary to ensure that all stakeholders are informed, engaged, and supportive of the migration.
Addressing these potential issues with careful planning, thorough testing, and adequate support can help organizations navigate the migration process successfully and fully reap the benefits of the MRP system.
Bringing it all together
If you’ve gotten to the bottom of this article, the process may seem alarmingly complex. Don’t worry! There are plenty of tools and best practices to help make the migration process far easier. The best thing one can do is to start the process by developing a plan for making it happen and getting by-in from your organization you can rely on.
When you’re ready to make the step to a true MRP management system, then it’s time to consider Aligni MRP. We’ve helped many firms just like yours make the transition to greater efficiency by helping firms better manage their data and processes.
Start your 30-day free trial
Helping You Make Great Things…Better.