Manufacturers need parts and materials to build products but they also need these materials in the right quantities. Companies also need them delivered at the right times to make sure production runs smoothly. This requires a process to oversee these operations. Inventory tracking is that process for manufacturers. It enables companies to monitor and manage their raw materials, work-in-progress (WIP), and finished goods throughout the production cycle.
The main objective of inventory tracking is to maintain optimal stock levels, reduce stockouts, and streamline operations. Manufacturers employ various techniques to achieve this, such as barcode scanning, RFID technology, and real-time data updates. This ensures accurate and efficient tracking of inventory movements.
Integration with other business processes, like sales and purchasing, facilitates seamless coordination and data synchronization. This integration, if done correctly, can help make a manufacturing organization more predictive in what it needs for future jobs. It provides this ability by combining order information and supply chain performance with historical consumption data to plan better for upcoming needs.
Inventory Tracking in Practice
The inventory tracking process begins with the setup and organization of the inventory management system. Manufacturers categorize items, assign unique identifiers such as SKUs or serial numbers, and establish a reliable framework for data entry. When raw materials or components arrive, they are recorded in the system, and quality checks are performed to ensure compliance with established standards.
A detailed Bill of Materials (BOM) is created for each product, listing all the required components and quantities needed for production. Work orders are then generated based on production schedules, and WIP tracking provides real-time updates on the progress of each order as it moves through various production stages.
For optimal stock management, manufacturers often employ the First-In, First-Out (FIFO) or Last-In, First-Out (LIFO) principles to manage material usage during production, ensuring older inventory is used first. Batch and serial number tracking allow for traceability and quality control, enabling manufacturers to identify specific batches or production runs. Finished goods are stored in designated areas, and barcode scanning or RFID technology is employed when shipping products to customers or moving them to distribution centers. The inventory tracking system is continually updated to reflect real-time stock levels and movements, providing accurate and timely information for decision-making.
Manufacturers also utilize demand forecasting based on historical data, sales orders, and market trends to predict future demand, aiding in production planning and maintaining optimal inventory levels. Setting reorder points for materials and maintaining safety stock levels helps avoid stockouts and ensures a smooth production process. Regular audits and cycle counts verify inventory accuracy, while effective supplier management ensures timely deliveries and high-quality materials. By continually analyzing inventory data, manufacturers can identify trends, optimize their supply chain, improve cost management, and meet customer demands more efficiently.
The Right Tools for the job
While it may seem like inventory tracking could be managed through spreadsheets, in practice the amount of data that needs to be tracked makes it difficult to do within a collection of tabs and sheets. To get more intelligence out of the data contained in the spreadsheet would require the development of carefully curated formulas and programming – all of which could be threatened by an errant overwriting of a few cells.
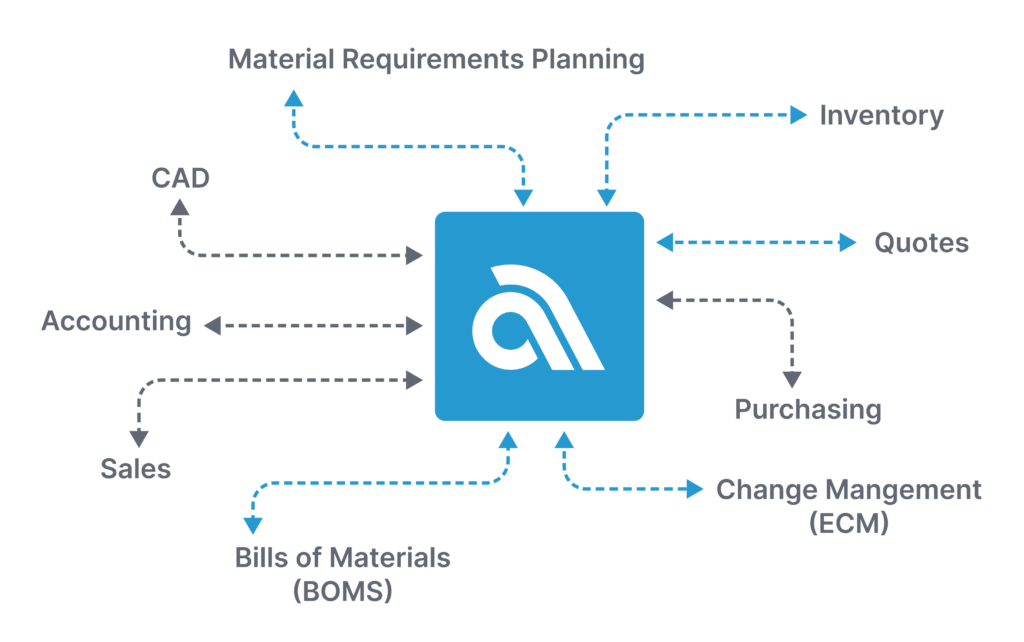
Effectively managing inventory also requires collaboration between several departments. This is another aspect where spreadsheets make the process more complex. Keeping the file or collection of files available to a number of parties within the firm is a sticky prospect. Protecting the file or just portions of the file is cumbersome to almost impossible. Both of these aspects mean firms who choose to track inventory with spreadsheets tend to leave a lot of efficiency, error-proofing and insight on the table.
Instead, most firms employ Material Requirements Planning (MRP) software to manage inventory, like Aligni MRP. These systems are built on an item master database that handles the varying amounts of data and their interconnections much more efficiently than spreadsheets.
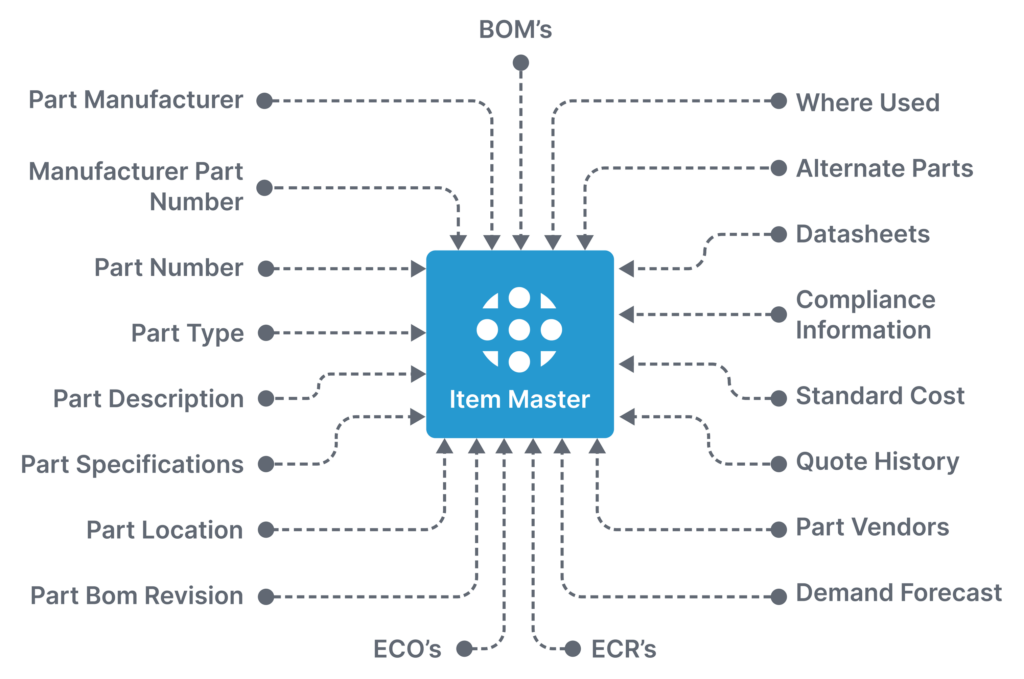
Material requirements planning systems also feature advanced capabilities that can help manage and create insights from the data in ways that would require custom formulas or programming in a spreadsheet-based system. For instance, MRP systems can reach across BOMs and production schedules to help supply chain managers understand inventory levels and even help determine which vendor may have the best availability and pricing for upcoming builds. These are just a few of the ways MRP systems not only streamline inventory tracking but enhance operational efficiency, reduce carrying costs, and ultimately, help manufacturers remain competitive in their markets. To learn more about MRP systems and their capabilities, investigate Aligni MRP.
Looking to get a better handle on your inventory? Want to get more out of it than you can with homegrown spreadsheets? Sign up for Aligni MRP today!
Start your 30-day free trial
Helping You Make Great Things…Better.