In the fast-paced world of electronics manufacturing, maintaining high product quality, regulatory compliance, and operational efficiency is critical to success. A Quality Management System (QMS) plays a central role in achieving these goals by standardizing processes, ensuring traceability, and driving continuous improvement. From component sourcing and PCB assembly to functional testing and final inspection, a well-implemented QMS ensures that every stage of production meets strict industry standards. Modern QMS solutions help manufacturers minimize defects, reduce costs, and enhance customer satisfaction. Here, we explore how QMS systems function within an electronics manufacturing environment, detailing their key components, benefits, and best practices for implementation.
What Is a QMS?
A quality management system is a structured framework of policies, processes, and procedures designed to ensure that an organization consistently meets customer and regulatory requirements while continuously improving its operations. It provides a systematic approach to managing quality through documentation, performance monitoring, and corrective actions. A well-implemented QMS enhances efficiency, reduces errors, and promotes customer satisfaction by standardizing workflows and fostering a culture of continuous improvement.
How Does QA and QC Integrate with a QMS System?
With seemingly competing processes like Quality Assurance (QA) and Quality Control (QC), it can be difficult to understand if these processes work together with a QMS, or in place of it. To quickly answer the question, a quality management system integrates quality assurance and quality control by providing an overarching structured framework that governs both proactive (QA) and reactive (QC) quality measures.
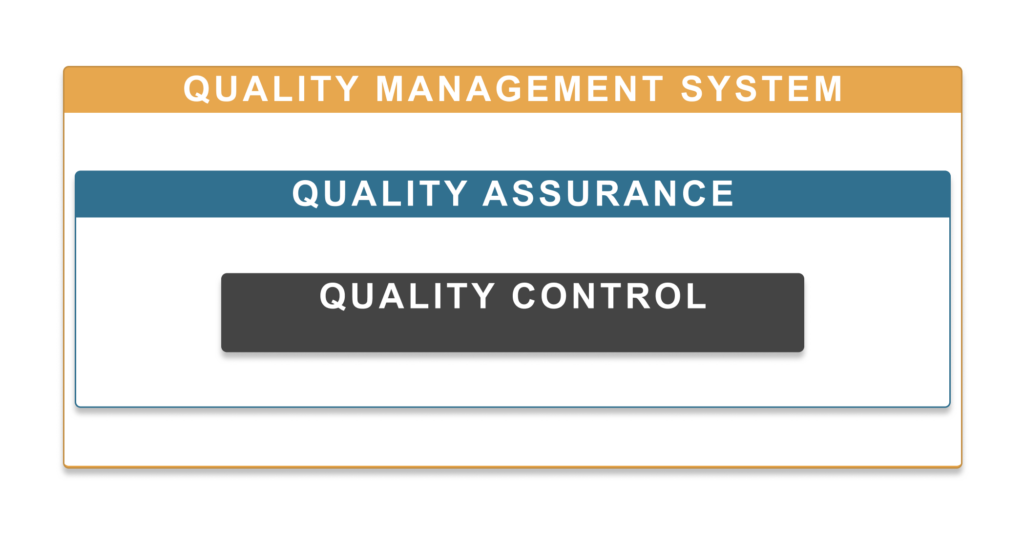
Quality Assurance and QMS
The quality assurance process focuses on preventing defects by establishing standardized processes, training, and continuous improvement initiatives. The QMS supports QA by defining quality policies, documenting best practices, and ensuring compliance with regulatory and industry standards. It also facilitates internal audits, risk management, and process optimization to maintain consistency in production or service delivery.
Quality Control and QMS
Quality control, on the other hand, is a reactive process that involves inspecting and testing products or services to identify defects before they reach customers. The QMS provides the necessary procedures, checklists, and corrective action protocols to standardize QC operations. It ensures that QC teams have clear guidelines on testing criteria, defect reporting, and resolution processes, allowing for effective feedback loops that drive process improvements.
Interaction Between QMS, QA, and QC
The QMS acts as the backbone that connects QA and QC, ensuring that preventive (QA) and corrective (QC) actions work together to enhance overall quality. It enables organizations to track quality metrics, analyze trends, and implement Corrective And Preventive Actions (CAPA) to minimize recurring issues. This integrated approach fosters continuous improvement and ensures compliance with regulatory and customer expectations.
Compliance-Driven vs. Performance-Driven QMS: Finding the Right Approach
Organizations often fall into one of two categories when implementing a QMS: compliance-driven or performance-driven. Understanding the distinction between these approaches can help businesses tailor their quality strategies to meet both regulatory obligations and operational goals.
Compliance-Driven QMS
A compliance-based QMS is primarily focused on meeting industry regulations and passing audits. This approach is often necessary in highly regulated industries such as medical devices, aerospace, and automotive manufacturing, where non-compliance can result in fines, recalls, or loss of certification. Characteristics of a compliance-driven QMS include:
- Strict adherence to ISO 9001, IATF 16949, ISO 13485, and other regulatory frameworks.
- Extensive documentation to demonstrate compliance during audits.
- Minimal process flexibility, as procedures are designed to meet external requirements rather than optimize operations.
While compliance-driven QMS ensures legal and regulatory adherence, it may not always lead to improved efficiency, innovation, or cost reduction.
Performance-Driven QMS
A performance-driven QMS goes beyond compliance and focuses on continuous improvement, efficiency, and competitive differentiation. Companies using this approach see quality as an enabler of operational excellence rather than just a regulatory obligation. Key aspects of a performance-driven QMS include:
- Data-driven decision-making, using quality metrics to optimize production processes.
- Lean and Six Sigma methodologies to systematically reduce defects and waste.
- Cross-functional collaboration, ensuring quality improvement is embedded across departments (engineering, production, procurement, etc.).
- Proactive risk management, addressing potential quality issues before they arise.
Many organizations find success in blending these approaches—starting with compliance as a foundation and then evolving toward a performance-driven QMS for sustained business growth.
What makes up a QMS Framework
To better understand what goes into a quality management system framework, we have specifically designed an example for electronics manufacturing. This framework helps ensure compliance with industry standards such as ISO 9001, IATF 16949 (automotive electronics), ISO 13485 (medical electronics), and IPC-A-610 (electronic assemblies) while optimizing processes for high-quality production.
Electronics Manufacturing QMS Framework
1. Quality Policy & Objectives
- Define a clear quality policy aligned with customer expectations, regulatory requirements, and industry standards.
- Establish measurable quality objectives, such as:
- Reducing defect rates (DPPM – Defective Parts Per Million)
- Improving First-Pass Yield (FPY)
- Enhancing On-Time Delivery (OTD) performance
- Reducing rework and scrap rates
- Communicate these objectives to all employees and stakeholders.
2. Document Control & Record Management
- Implement revision-controlled documentation for:
- Standard Operating Procedures (SOPs)
- Work Instructions (WIs)
- Process Flow Diagrams (PFDs)
- Quality Control Plans (QCPs)
- Material Safety Data Sheets (MSDS)
- Component datasheets and supplier specifications
- Maintain records of:
- Inspection and testing logs
- Calibration records
- Non-Conformance Reports (NCRs)
- Corrective And Preventive Actions (CAPA)
3. Risk Management & Failure Analysis
- Conduct Failure Mode and Effects Analysis (FMEA) to anticipate potential failures in:
- PCB Assembly (PCBA)
- Surface Mount Technology (SMT)
- Through-hole soldering
- Wiring and harness assembly
- Functional testing
- Implement risk mitigation strategies such as:
- Design For Manufacturing (DFM) and Design For Testability (DFT)
- Process Failure Mode and Effects Analysis (PFMEA)
- Statistical Process Control (SPC) for defect prevention
4. Supplier & Component Quality Management
- Define supplier qualification criteria:
- Material composition compliance (e.g., RoHS, REACH, UL certification)
- Capability audits for PCB manufacturers, component suppliers, and contract manufacturers
- Vendor scorecards based on:
- On-time delivery performance
- Defect rates
- Responsiveness to corrective actions
- Implement Incoming Quality Control (IQC) for raw materials:
- Visual and dimensional inspection
- Electrical testing of components
5. Production Process Controls
a) Manufacturing Process Standardization
- Define process parameters for:
- Surface Mount Technology (SMT) soldering
- Wave soldering
- Selective soldering
- Conformal coating application
- Electromechanical assembly
- Ensure compliance with IPC-A-610 (Acceptability of Electronic Assemblies).
b) In-Process Quality Control (IPQC)
- Real-time Automated Optical Inspection (AOI) for solder defects.
- X-ray inspection for hidden solder joints (e.g., BGA components).
- Functional Testing (FCT) to verify circuit performance.
- Environmental stress testing (e.g., thermal cycling, humidity, vibration tests).
6. Quality Control & Defect Management
- Implement Defect Tracking System (DTS) using:
- Automated defect logging from AOI, ICT (In-Circuit Test), and FCT.
- Real-time dashboards displaying yield and defect trends.
- Root Cause Analysis (RCA) methods such as 5 Whys and Fishbone Diagrams.
- Define criteria for rework vs. scrap based on defect severity.
- Maintain strict Electrostatic Discharge (ESD) protection measures.
7. Customer Feedback & Complaint Handling
- Failure analysis of returned products.
- Implement 8D (Eight Disciplines) problem-solving methodology.
- Define corrective action timelines based on issue severity.
8. Compliance & Regulatory Requirements
- Ensure adherence to:
- ISO 9001 (General QMS)
- IATF 16949 (Automotive electronics manufacturing)
- ISO 13485 (Medical electronics)
- IPC-A-610 (Electronic assemblies standards)
- RoHS (Restriction of Hazardous Substances Directive)
- REACH (EU chemical safety standards)
- UL (Underwriters Laboratories certification)
- Maintain traceability records for regulatory audits.
9. Internal & External Audits
- Conduct regular internal process audits using:
- Layered Process Audits (LPA)
- 5S workplace organization checks
- Calibration audits for test equipment
- Prepare for third-party and customer audits:
- Documentation reviews
- Compliance verification with industry standards
10. Training & Competency Development
- Train employees in:
- IPC-A-610 certification for PCB assembly inspection.
- ESD handling procedures.
- Root Cause Analysis (RCA) methodologies.
- Equipment calibration and maintenance.
- Implement competency matrices to track employee skills.
11. Continuous Improvement (Kaizen & Six Sigma)
- Data-driven decision-making using:
- Statistical Process Control (SPC) for real-time monitoring.
- Six Sigma tools (DMAIC – Define, Measure, Analyze, Improve, Control) to reduce defects.
- Plan-Do-Check-Act (PDCA) cycles for process improvements.
- Encourage employee-led Kaizen events for waste reduction.
12. Corrective & Preventive Actions (CAPA)
- Implement structured CAPA processes:
- Corrective actions: Address recurring defects in SMT assembly, soldering, testing, etc.
- Preventive actions: Use design improvements, supplier quality checks, and process refinements to prevent future failures.
- Monitor CAPA effectiveness using Key Performance Indicators (KPIs).
This Electronics Manufacturing QMS Framework is designed to ensure process consistency, regulatory compliance, and product reliability. It is also an exhaustive example of what a framework could look like. Every market sector and product’s quality requirements are different. Some may only require a portion of the depth of planning shown above. Others may require even greater detail and levels.
Additionally, startups and SMBs may need to make a plan to build into the levels shown above after establishing the broad strokes of the program and learning what is truly necessary for their needs. Regardless of the level of detail a QMS framework provides, by integrating risk management, supplier quality, process controls, and continuous improvement, electronics manufacturers can achieve higher yields, lower defect rates, and increased customer satisfaction.
Managing QMS Complexity with Proper Tools
Managing a quality management system with purpose-built software is the most effective way to ensure compliance, improve efficiency, and maintain high-quality standards. Unlike traditional paper-based or manual methods, QMS software centralizes document control, ensuring that only authorized personnel can access and modify critical quality documents while maintaining version control and approval workflows. This prevents outdated procedures from being used, reducing the risk of nonconformance.
Additionally, QMS software structures workflows for key processes such as CAPA, audits, nonconformance tracking, and change management, minimizing human error and ensuring that compliance tasks are completed on time. By reducing paperwork, automating repetitive tasks, and improving resource allocation, QMS software significantly lowers operational costs while increasing efficiency.
QMS software also enhances supplier quality and compliance management by providing a schedule for supplier audits, qualification processes, and performance tracking. It ensures traceability of incoming materials, helping manufacturers enforce compliance with RoHS, REACH, UL, and industry-specific regulations. Additionally, the system simplifies internal and external audits by maintaining structured audit trails and compliance reports, ensuring readiness for ISO certifications, FDA inspections, and customer audits.
Beyond compliance, QMS software improves communication and collaboration by providing a centralized platform for quality teams, production staff, and suppliers to work together seamlessly. Automated training systems keep employees up to date on QMS procedures and regulatory requirements, while integrated messaging and notifications ensure that corrective actions and quality updates reach all relevant stakeholders. Cloud-based QMS solutions further improve scalability and accessibility, allowing real-time data sharing across multiple locations and ensuring automatic updates to keep up with evolving industry standards.
It must be noted that while there are many purpose-built QMS systems on the market, the level of complexity and capability these systems provide may be overwhelming, especially for startups and SMBs. In these scenarios where only the fundamental QMS functionality is needed, seeking out only the required capabilities within adjacent business systems like Material Requirements Planning systems (MRP) may be a better fit for the organization.
Taking the Next Steps
A properly designed, maintained, and executed QMS framework enhances efficiency, compliance, data-driven decision-making, and cost-effectiveness over the production and even product lifecycle. By properly delineating workflows, and centralizing data management, companies can reduce operational risks, streamline quality processes, and achieve continuous improvement in manufacturing operations.
If you are looking to get serious about your quality processes, now is the time to build a proper quality management framework for your organization. But first, it is time to invest in a purpose-built system that can help you execute the plan: Aligni MRP. Sign up today!
Start your 30-day free trial
Join over 4,000 teams that are managing their manufacturing with Aligni.