For simple products, a bill of materials (BOM) can be easily managed with a spreadsheet. When the complexity increases, it goes from simple rows and columns to much more. Then it’s time for software that’s built for the purpose, rather than fitting all that data and management into a tool that hasn’t been optimized for the job.
What Makes a BOM Complex?
Bill of Materials can become complex due to various factors. These factors are based on what kind of product is being produced, where the product and its sub-assemblies are being built, and the amount of variability the product provides or undergoes in its lifecycle. Here are some common elements that can contribute to increased complexity in manufacturing BOMs:
A Large Number of Product Variants
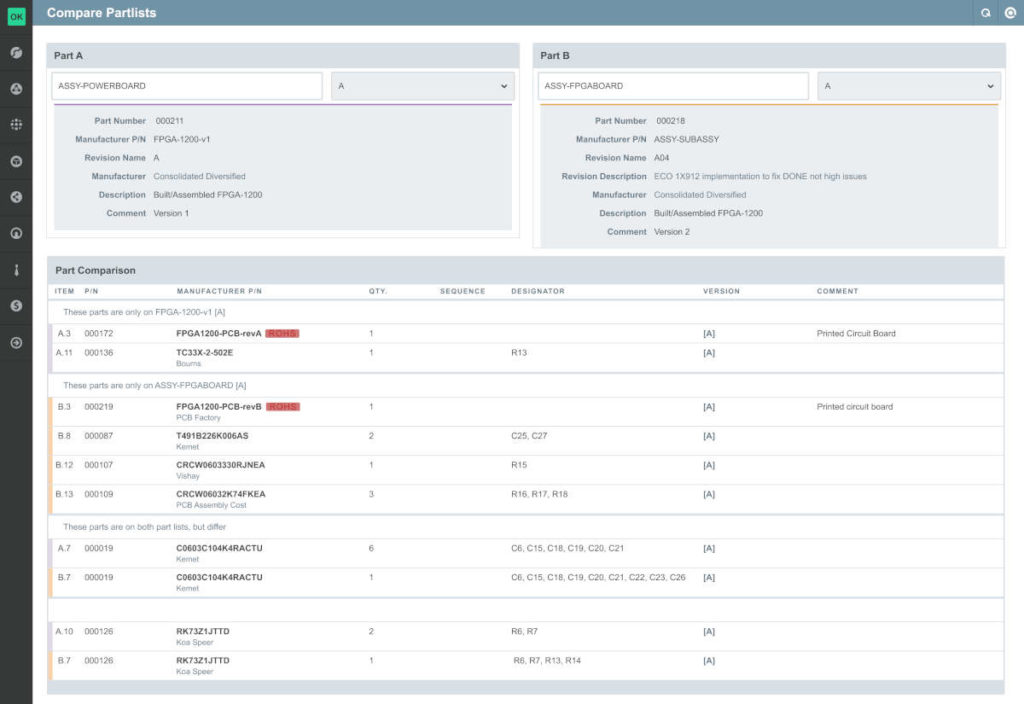
When a product has multiple variants or configurations, it leads to a more complex BOM. Each variant may have unique components or variations in the assembly process. All these have to be managed separately in the same system without the features or specifications of each colliding.
Utilizing Subassemblies
The use of subassemblies, where a product’s individual components are grouped and assembled separately before being integrated into the final product, can increase BOM complexity. This is even more true when these components are built through sub-contractors. Analyzing what goes into these assemblies is not something that can easily be done with spreadsheets, especially when there are variants within the subassemblies.
Managing Multi-Level BOMs
BOMs that have multiple levels, with nested subassemblies, components, and raw materials can become intricate. Managing dependencies and relationships between different levels adds to the complexity.
The Use of Phantom BOMs
Phantom BOMs represent assemblies that are used for structuring and planning but are not physically assembled. These virtual assemblies add complexity to the BOM structure as they start out as exercises or forks of current products. Many times these have to be independently managed and sometimes turned into production-ready versions, all without confusion with current products.
Tracking Engineering Changes
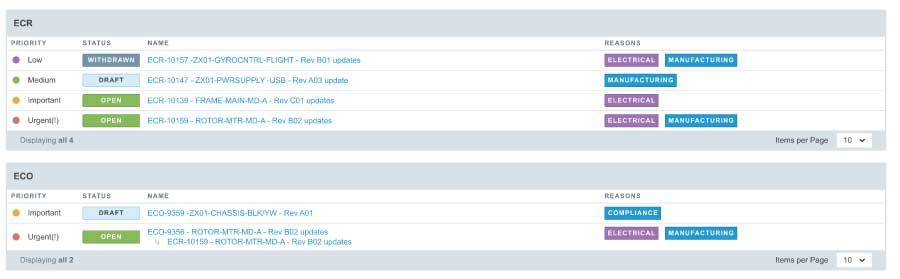
Frequent changes to the design or specifications of a product can result in multiple versions of the BOM, each corresponding to a specific revision. Managing and tracking these changes increases complexity, as well as alerting others in the organization that changes have occurred to the parts lists for the product.
Cataloging Material Variations
The use of different materials for the same component or assembly, such as different grades of metal or plastic, adds complexity to the BOM as each variation needs to be accounted for, but kept separate from other versions of the product.
Overseeing Regulatory Compliance
Products that need to comply with specific regulations may require additional components or processes to meet those standards, leading to a more complex BOM. This is especially true if the company is subject to compliance audits by governments or customers.
Controlling for supplier variability
Different suppliers may provide components with slight variations, and managing these differences in the BOM can increase complexity, especially when alternative sources are used.
Storing Documentation and Instructions
Including detailed instructions, drawings, and other documentation for each component or assembly in the BOM can contribute to complexity, but it is crucial for ensuring accurate manufacturing.
BOMs in MRP: It’s All about the Database
When there’s a lot to manage with BOMs, it’s important to have the right tools for the job. Software systems like Material Requirements Planning (MRP) systems built on databases outperform spreadsheets in handling complex bills of materials due to their inherent capabilities at handling large amounts of interconnected data. One key advantage MRP systems have lies in data integrity; databases enforce relationships between entities, mitigating errors and redundancies. Moreover, they allow for data normalization, minimizing redundancy and facilitating efficient organization.
Scalability is another notable strength of MRP systems, particularly crucial as BOM complexity increases. They can efficiently manage large volumes of data, a task where spreadsheets may fall short. Version control, an essential aspect in dynamic manufacturing environments, is more robust in MRP systems. They provide comprehensive tracking of changes, managing versions, and maintaining a history of BOM revisions, as many systems like Aligni MRP, have integrated Engineering Change Management (ECM) systems that easily pass on updates to the company’s BOMs.
Concurrency, or the ability to handle simultaneous data access and updates, is managed more effectively in MRP systems. Security features, including user access controls, protect sensitive BOM data, ensuring only authorized personnel can modify or view specific information.
MRP systems also offer superior querying capabilities, enabling flexible and efficient data retrieval and analysis. This proves beneficial for generating reports, conducting analyses, and extracting insights from intricate BOM structures. Integration with other enterprise systems, such as ERP or PLM systems, is smoother with MRP, allowing seamless data flow across organizational units.
Consistency is enforced through database rules, maintaining data accuracy and coherence. Collaboration is enhanced as multiple users can work on different aspects of the BOM simultaneously. This collaborative feature is particularly valuable in manufacturing environments where various teams contribute to BOM development and maintenance.
How to Recognize When It’s Time to Migrate to an MRP System
Several indicators suggest that a company should contemplate transitioning from spreadsheet-based bill of materials management to a dedicated MRP system.
- A notable signal is the increasing complexity of products and BOMs, where spreadsheets may struggle to provide the required structure for managing multiple variants, subassemblies, and dependencies effectively.
- Frequent changes and revisions to BOMs, whether due to design updates, engineering changes, or market demands, are better handled by an MRP system equipped with robust version control capabilities.
- Challenges in inventory management, including difficulties in tracking and optimizing inventory levels, can be alleviated by the automation features of an MRP system, which streamlines inventory tracking, reorder points, and replenishment processes.
- Production planning and scheduling issues, especially in scenarios involving various components, lead times, and dependencies, often point towards the limitations of spreadsheets in handling complexity.
- As the number of Stock Keeping Units (SKUs) and product variations increases, managing this diversity in spreadsheets becomes cumbersome, making an MRP system a more suitable solution.
- Collaboration challenges arising from multiple teams or departments involved in BOM management are better addressed by MRP systems, which typically offer collaborative features to facilitate seamless teamwork.
- Data accuracy and integrity concerns associated with spreadsheets are mitigated by MRP systems that enforce consistency and integrity, reducing the risk of errors in BOMs.
Finally, growing customer demands for faster response times, customized products, or detailed documentation underscore the benefits of an MRP system in enhancing overall operational efficiency to meet evolving market requirements.
If a company identifies one or more of these signs, it may be prudent to explore the adoption of an MRP system for more effective BOM management and operational optimization.
Bringing It All Together
While spreadsheets have their merits, MRP systems built on databases emerge as a more robust and suitable choice for managing complex BOMs in manufacturing, offering a comprehensive set of features to address the intricacies of the process. If it looks like your homegrown system is straining to effectively manage bills of material with increasing complexity, then it’s time to consider migrating to an MRP system. It’s time to sign up for Aligni MRP today!
Start your 30-day free trial
Helping You Make Great Things…Better.